Parallel clamping device and method for robot end
A robot and parallel clamping technology, applied in the direction of chucks, manipulators, manufacturing tools, etc., can solve the problems of inconvenient maintenance, high equipment cost, poor automatic workpiece centering ability, etc., to improve production efficiency and degree of automation, centering High stability and synchronization, high clamping accuracy
- Summary
- Abstract
- Description
- Claims
- Application Information
AI Technical Summary
Problems solved by technology
Method used
Image
Examples
Embodiment
[0028] In this embodiment, a parallel clamping device for the end of the robot, such as figure 1 or figure 2 As shown, it includes driving cylinder 1, parallel clamping mechanism and two sets of end clamping mechanisms. The two sets of end clamping mechanisms are respectively arranged on both sides of the parallel clamping mechanism. connect.
[0029] Such as image 3 As shown, the parallel clamping mechanism includes a compression flange 2, a central shaft 3, a rotating seat 4, an adjustment rod 5, and an adjustment base plate 6. The compression flange is fixedly connected to the top of the central shaft, and the bottom of the central shaft is fixedly connected to the adjustment base plate. The swivel seat is connected with the outer periphery of the central shaft through the central bearing 7, the bottom of the compression flange is pressed against the inner ring of the central bearing, and the top surface of the swivel seat is connected with the terminal clamping mechani...
PUM
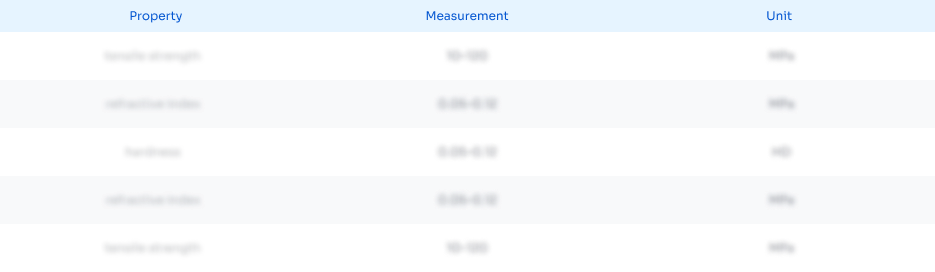
Abstract
Description
Claims
Application Information

- R&D
- Intellectual Property
- Life Sciences
- Materials
- Tech Scout
- Unparalleled Data Quality
- Higher Quality Content
- 60% Fewer Hallucinations
Browse by: Latest US Patents, China's latest patents, Technical Efficacy Thesaurus, Application Domain, Technology Topic, Popular Technical Reports.
© 2025 PatSnap. All rights reserved.Legal|Privacy policy|Modern Slavery Act Transparency Statement|Sitemap|About US| Contact US: help@patsnap.com