An air filter capable of separating oil and vapor
An oil-vapor separation and air filter technology, applied in the field of air filters, can solve the problems of increased exhaust resistance of crankcases, blue smoke from mufflers, and excessive exhaust emissions, so as to reduce exhaust emissions, prevent waste of oil, and reduce costs. Effect
- Summary
- Abstract
- Description
- Claims
- Application Information
AI Technical Summary
Problems solved by technology
Method used
Image
Examples
Embodiment Construction
[0019] Such as Figures 1 to 5 As shown, an air filter capable of oil-vapor separation includes a base and an air filter body mounted on the base, wherein the base includes a base body 1 and a baffle 3, and the air filter body is installed on the base body 1 on the baffle 3 On one side, the baffle 3 is closely fitted to the base body 1 and there is a hollow cavity between the two. The close fit is used here to realize the sealing between the baffle 3 and the base body 1 to prevent leakage between the two. Gas, the cavity between the baffle plate 3 and the base body 1 is used as an oil-vapor separation chamber 4 to cool the exhaust gas with oil vapor and oil droplets entering it to separate the oil-vapor (preferably the cavity is a flat cavity, so that after the exhaust gas enters the cavity, the contact effect with the cavity wall is good, and the cooling effect is also good), the side of the base body 1 away from the baffle 3 is provided with an oil vapor inlet channel 5 and ...
PUM
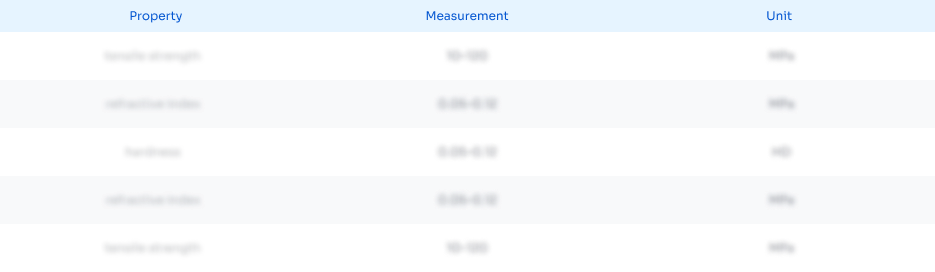
Abstract
Description
Claims
Application Information

- R&D
- Intellectual Property
- Life Sciences
- Materials
- Tech Scout
- Unparalleled Data Quality
- Higher Quality Content
- 60% Fewer Hallucinations
Browse by: Latest US Patents, China's latest patents, Technical Efficacy Thesaurus, Application Domain, Technology Topic, Popular Technical Reports.
© 2025 PatSnap. All rights reserved.Legal|Privacy policy|Modern Slavery Act Transparency Statement|Sitemap|About US| Contact US: help@patsnap.com