A Fatigue Life Design Method for Aircraft Bolts
A design method and fatigue life technology, applied in the direction of calculation, special data processing applications, instruments, etc., can solve the problem of not considering the influence of bolt fatigue life, and achieve the effect of convenient calculation process, clear analysis steps and correct theoretical basis
- Summary
- Abstract
- Description
- Claims
- Application Information
AI Technical Summary
Problems solved by technology
Method used
Image
Examples
Embodiment 1
[0036] A fatigue life design method for aircraft bolts, comprising the following steps:
[0037] Known: bolt material is medium-strength steel, bolt diameter D=20mm, bolt heat treatment σ b It is 1103MPa. Target life flight times N m =10000, fatigue reliability factor FRF=2.
[0038] Step 1. Using finite element software, determine the tensile stress σ of the bolt under each peak and trough in the aircraft load spectrum: Among them, F is the axial load borne by the bolt, and D is the diameter of the bolt;
[0039] Step 2. Using finite element software, determine the shear stress τ of the bolt under each peak and trough in the aircraft load spectrum: ; Among them, Q is the shear load borne by the bolt, and D is the diameter of the bolt;
[0040] Step 3. Using the fourth theory of strength, determine the equivalent tensile stress σ of the bolt under each peak and trough in the aircraft load spectrum req : Among them, σ is the bolt tensile stress, τ is the bolt shear st...
Embodiment 2
[0051] A fatigue life design method for aircraft bolts, comprising the following steps:
[0052] Known: Bolt material is medium-strength steel, bolt diameter D=18mm, bolt heat treatment σ b It is 1103MPa. Target life flight times N m =10000, fatigue reliability factor FRF=2.
[0053] Step 1. Using finite element software, determine the tensile stress σ of the bolt under each peak and trough in the aircraft load spectrum: Among them, F is the axial load borne by the bolt, and D is the diameter of the bolt;
[0054] Step 2. Using finite element software, determine the shear stress τ of the bolt under each peak and trough in the aircraft load spectrum: Among them, Q is the shear load borne by the bolt, and D is the diameter of the bolt;
[0055] Step 3. Using the fourth theory of strength, determine the equivalent tensile stress σ of the bolt under each peak and trough in the aircraft load spectrum req : Among them, σ is the bolt tensile stress, τ is the bolt shear stre...
Embodiment 3
[0075] A fatigue life design method for aircraft bolts, comprising the following steps:
[0076] Known: bolt material is titanium alloy, bolt diameter D=18mm, bolt heat treatment σ b It is 1103MPa. Target life flight times N m =10000, fatigue reliability factor FRF=2.
[0077] Step 1. Using finite element software, determine the tensile stress σ of the bolt under each peak and trough in the aircraft load spectrum: Among them, F is the axial load borne by the bolt, and D is the diameter of the bolt;
[0078] Step 2. Using finite element software, determine the shear stress τ of the bolt under each peak and trough in the aircraft load spectrum: Among them, Q is the shear load borne by the bolt, and D is the diameter of the bolt;
[0079]Step 3. Using the fourth theory of strength, determine the equivalent tensile stress σ of the bolt under each peak and trough in the aircraft load spectrum req : Among them, σ is the bolt tensile stress, τ is the bolt shear stress;
[...
PUM
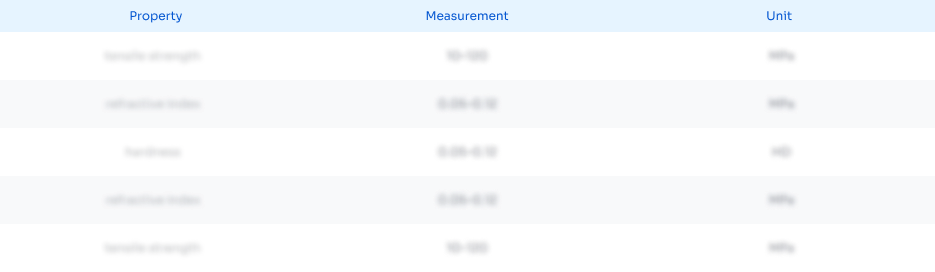
Abstract
Description
Claims
Application Information

- R&D
- Intellectual Property
- Life Sciences
- Materials
- Tech Scout
- Unparalleled Data Quality
- Higher Quality Content
- 60% Fewer Hallucinations
Browse by: Latest US Patents, China's latest patents, Technical Efficacy Thesaurus, Application Domain, Technology Topic, Popular Technical Reports.
© 2025 PatSnap. All rights reserved.Legal|Privacy policy|Modern Slavery Act Transparency Statement|Sitemap|About US| Contact US: help@patsnap.com