Coupling and middle chucking, conduction testing, encoding and die arraying device of detonator and automatic control method
A technology of conduction test and bayonet card, which is applied in the direction of detonators and offensive equipment, can solve the problems of difficult to ensure the accuracy of process connection, many components involved in human participation, and low degree of automation, so as to reduce the chance of personnel being injured, Low cost and the effect of improving production efficiency
- Summary
- Abstract
- Description
- Claims
- Application Information
AI Technical Summary
Problems solved by technology
Method used
Image
Examples
Embodiment Construction
[0020] The detonator bayonet clamping waist and conduction testing device provided by the present invention is divided into a workpiece conveying mechanism and an operating station by a protective plate 11 . The operating station refers to the bayonet card waist station and the conduction mold row station, which are arranged at intervals to facilitate the transfer of workpieces between the two processes.
[0021] Such as figure 1 , image 3 As shown, the workpiece conveying mechanism includes a horizontal conveying device and a vertical conveying device. Among them, the horizontal conveying device includes an upper belt conveyor 2 and a lower belt conveyor 1, which are respectively responsible for the delivery of the real mold 3 and the empty mold 21 equipped with detonators to be processed, as well as the real code box 10 and the empty code box for encoding the processed detonators. 9 delivery.
[0022] Such as Figure 1~3 As shown, the bayonet card waist parting device o...
PUM
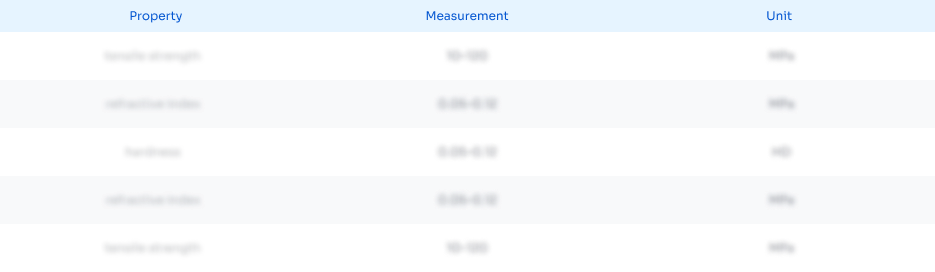
Abstract
Description
Claims
Application Information

- R&D Engineer
- R&D Manager
- IP Professional
- Industry Leading Data Capabilities
- Powerful AI technology
- Patent DNA Extraction
Browse by: Latest US Patents, China's latest patents, Technical Efficacy Thesaurus, Application Domain, Technology Topic, Popular Technical Reports.
© 2024 PatSnap. All rights reserved.Legal|Privacy policy|Modern Slavery Act Transparency Statement|Sitemap|About US| Contact US: help@patsnap.com