Robotic Arm Control
A control device, robotic arm technology, applied in the direction of manipulator, program control, general control system, etc., can solve problems such as changing programs
- Summary
- Abstract
- Description
- Claims
- Application Information
AI Technical Summary
Problems solved by technology
Method used
Image
Examples
Embodiment approach
[0028] figure 1 It is a figure which shows the structure of the robot arm control system in which the embodiment of the robot arm control apparatus which concerns on this invention is used. The manipulator control system has a three-dimensional vision sensor 1, a teaching box (T / B) 2, a computer 3, a manipulator control device 4 and a manipulator 5, and the manipulator 5 is used to grasp and move the workpiece 6.
[0029] The three-dimensional vision sensor 1 serving as a workpiece detection unit includes an imaging unit 11 that generates image data by imaging, and a robot arm coordinate generation unit 12 that processes the image data generated by the imaging unit 11 to generate coordinate data of the robot arm.
[0030] The robotic arm control device 4 has: an interface (I / F) 41, which is used to transmit / receive data with the three-dimensional vision sensor 1, T / B 2, and computer 3; a storage unit 42, which stores various parameters 421 and action descriptions; The program...
PUM
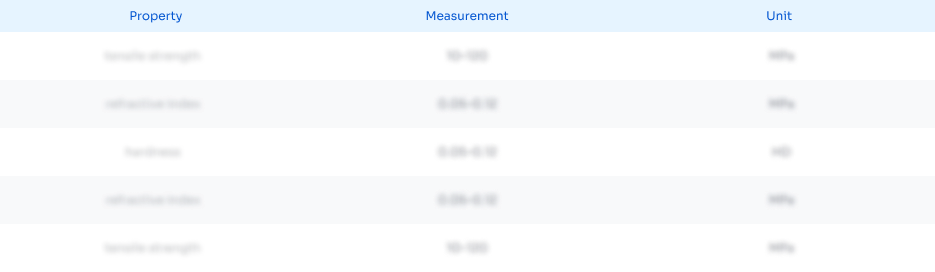
Abstract
Description
Claims
Application Information

- R&D
- Intellectual Property
- Life Sciences
- Materials
- Tech Scout
- Unparalleled Data Quality
- Higher Quality Content
- 60% Fewer Hallucinations
Browse by: Latest US Patents, China's latest patents, Technical Efficacy Thesaurus, Application Domain, Technology Topic, Popular Technical Reports.
© 2025 PatSnap. All rights reserved.Legal|Privacy policy|Modern Slavery Act Transparency Statement|Sitemap|About US| Contact US: help@patsnap.com