Robot spray workpiece surface modeling method
A surface modeling and robot technology, which is applied in the directions of manipulators, spray devices, manufacturing tools, etc., can solve problems such as inability to use complex curved workpiece surfaces for spraying operations, low precision, and inability to apply the angle between the normal vectors of the spraying surfaces.
- Summary
- Abstract
- Description
- Claims
- Application Information
AI Technical Summary
Problems solved by technology
Method used
Image
Examples
Embodiment Construction
[0050] The present invention will be further described below in conjunction with the drawings and specific embodiments.
[0051] The implementation steps of the present invention are mainly composed of three parts: connecting triangles into smaller plane pieces, establishing plane piece connection diagram FPAG, and merging smaller plane pieces into several new larger plane pieces. The specific implementation is as follows:
[0052] 1. Triangular faces are connected into smaller flat pieces
[0053] After inputting the CAD data of the workpiece in the engineering application software (such as GID7.2), use the triangle output function of the software to directly triangulate the workpiece. The specific steps of triangular meshing of workpiece surface are as follows:
[0054] ① According to the CAD model of the workpiece, divide the surface of the workpiece into a triangular mesh;
[0055] ② After the division is completed, the triangular mesh surface is obtained to approximate the origin...
PUM
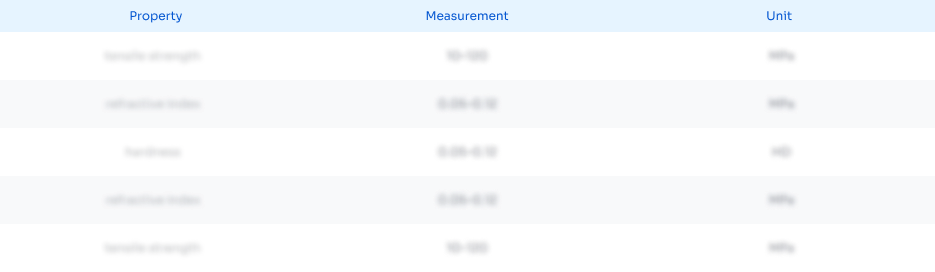
Abstract
Description
Claims
Application Information

- R&D
- Intellectual Property
- Life Sciences
- Materials
- Tech Scout
- Unparalleled Data Quality
- Higher Quality Content
- 60% Fewer Hallucinations
Browse by: Latest US Patents, China's latest patents, Technical Efficacy Thesaurus, Application Domain, Technology Topic, Popular Technical Reports.
© 2025 PatSnap. All rights reserved.Legal|Privacy policy|Modern Slavery Act Transparency Statement|Sitemap|About US| Contact US: help@patsnap.com