Laser force measuring system for double-probe atomic force microscope
An atomic force microscope and dual-probe technology, applied in scanning probe technology, instruments, etc., can solve the problems of not having a probe force measurement system and not being able to realize three-dimensional operation of nanostructures
- Summary
- Abstract
- Description
- Claims
- Application Information
AI Technical Summary
Problems solved by technology
Method used
Image
Examples
specific Embodiment approach 1
[0014] Specific implementation mode 1: Combination figure 1 with figure 2 To illustrate this embodiment, the laser force measurement system for dual-probe atomic force microscopes in this embodiment includes a first laser mechanics subsystem and a second laser mechanics subsystem. The first laser mechanics subsystem is used to detect double The signal of the first probe arm of the probe atomic force microscope, the second laser mechanics subsystem is used to detect the signal of the second probe arm of the double probe atomic force microscope, the first laser mechanics subsystem and the second laser mechanics The structure of the system is the same. The first laser mechanics subsystem includes a laser angle adjustment mechanism 1, a laser 2, an incident light convex lens 9, and an incident convex lens adjustment mechanism 4 used to adjust the position of the incident light convex lens 9. Mirror 8, reflective laser convex lens 5, reflective convex lens adjustment mechanism 6 fo...
specific Embodiment approach 2
[0018] Specific implementation manner two: combination figure 1 with figure 2 To explain this embodiment, the difference between this embodiment and the laser force measurement system for dual-probe atomic force microscopes described in the first embodiment is: in the first laser mechanics subsystem, the laser light emitted by the laser 2 passes through the first probe The laser light reflected by the needle tip of the arm and the laser light reflected by the mirror 8 are in the same plane, and the plane is the S1 surface; in the second laser mechanics subsystem, the laser light emitted by the laser 2 passes through the needle tip of the first probe arm The reflected laser light and the laser light reflected by the mirror 8 are in the same plane, and the plane is the S2 plane.
[0019] The lasers in each laser mechanics subsystem are in the same plane. This layout can save space so that other test or control systems can be added to achieve more functions.
specific Embodiment approach 3
[0020] Specific implementation mode three: combination figure 1 with figure 2 To describe this embodiment, the difference between this embodiment and the laser force measurement system for a dual-probe atomic force microscope described in the second embodiment is that the S1 surface and the S2 surface overlap.
[0021] This layout can save space to the greatest extent.
PUM
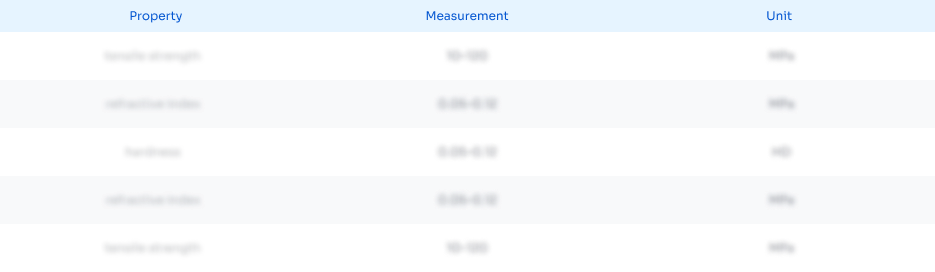
Abstract
Description
Claims
Application Information

- R&D Engineer
- R&D Manager
- IP Professional
- Industry Leading Data Capabilities
- Powerful AI technology
- Patent DNA Extraction
Browse by: Latest US Patents, China's latest patents, Technical Efficacy Thesaurus, Application Domain, Technology Topic, Popular Technical Reports.
© 2024 PatSnap. All rights reserved.Legal|Privacy policy|Modern Slavery Act Transparency Statement|Sitemap|About US| Contact US: help@patsnap.com