Tool mechanism for clamping frame workpiece of robot workstation
A technology of workstations and robots, applied in auxiliary devices, manufacturing tools, metal processing equipment, etc., can solve problems such as troublesome positioning of parts, unstable quality, and large human factors, and achieve improved work efficiency, reduced idle time, and ingenious structure reasonable effect
- Summary
- Abstract
- Description
- Claims
- Application Information
AI Technical Summary
Problems solved by technology
Method used
Image
Examples
Embodiment Construction
[0032] The present invention will be further described below in conjunction with the accompanying drawings and embodiments.
[0033] figure 2 , image 3 , Figure 4 , Figure 5 It shows a frame-shaped workpiece clamping tooling mechanism of a robot workstation, which includes a frame-shaped workpiece support that matches the frame-shaped workpiece, and the frame-shaped workpiece support 2 is connected to the main support 1 of the workbench of the robot workstation. Frame type workpiece support comprises four frame supports 201 and center support 202 that are fixedly connected, respectively is provided with frame type workpiece 3 (such as figure 1 The frame positioning blocks 4 matched with each frame shown in ) are provided with a clamping cylinder 5 on the inside of each frame positioning block 4, and the clamping cylinder 5 is fixedly connected with the center bracket 202, so The ejector rod of the jacking cylinder 5 can stably fix and position the four frames 301 of th...
PUM
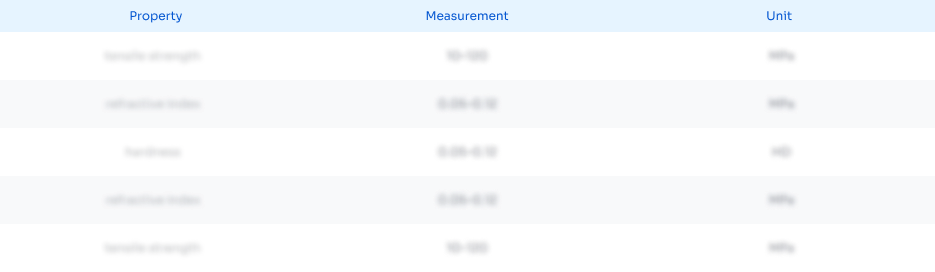
Abstract
Description
Claims
Application Information

- R&D
- Intellectual Property
- Life Sciences
- Materials
- Tech Scout
- Unparalleled Data Quality
- Higher Quality Content
- 60% Fewer Hallucinations
Browse by: Latest US Patents, China's latest patents, Technical Efficacy Thesaurus, Application Domain, Technology Topic, Popular Technical Reports.
© 2025 PatSnap. All rights reserved.Legal|Privacy policy|Modern Slavery Act Transparency Statement|Sitemap|About US| Contact US: help@patsnap.com