Preparation method of carbon-cladding Fe3O4 microsphere wave-absorbing material
A wave-absorbing material and carbon-coated technology, which is applied in the preparation/purification of carbon, chemical instruments and methods, oxides of ferrous iron, etc., can solve the problems of low dielectric constant, poor electromagnetic wave absorption, and difficult to achieve impedance matching, etc. Problems, to achieve the effect of enhancing wave-absorbing performance, improving impedance matching, and enhancing electromagnetic wave absorbing performance
- Summary
- Abstract
- Description
- Claims
- Application Information
AI Technical Summary
Problems solved by technology
Method used
Image
Examples
specific Embodiment approach 1
[0013] Specific implementation mode 1: In this implementation mode, carbon-coated Fe 3 o 4 The preparation method of the microsphere absorbing material is carried out according to the following steps:
[0014] 1. Preparation of Fe 3 o 4 Microspheres: 1~5g of FeCl 3 ·6H 2 Dissolve O in 50-100mL of organic solvent, stir evenly to obtain solution A; dissolve 1-5g of precipitant in 50-100mL of organic solvent, stir uniformly to obtain solution B, mix the obtained solution A with solution B, Stir evenly to obtain a mixed solution, put the obtained mixed solution into a polytetrafluoroethylene high-pressure reactor, and react at 100-200°C for 12-24 hours to obtain the product A, then wash the obtained product A with distilled water, and then wash it with absolute ethanol Product A was washed and finally dried to obtain Fe 3 o 4 Microspheres;
[0015] 2. Fe coated with phenolic resin 3 o 4 Preparation of microspheres: 0.5 to 2 g of Fe obtained in step 1 3 o 4 Put the micr...
specific Embodiment approach 2
[0017] Embodiment 2: This embodiment is different from Embodiment 1 in that: the organic solvent described in step 1 is one of ethylene glycol and glycerin or a mixture of the two in any ratio. Others are the same as in the first embodiment.
specific Embodiment approach 3
[0018] Specific embodiment three: the difference between this embodiment and specific embodiment one or two is that the precipitant described in step one is one or more of anhydrous sodium acetate, crystalline sodium acetate, and sodium citrate in any ratio. mixture. Others are the same as in the first or second embodiment.
PUM
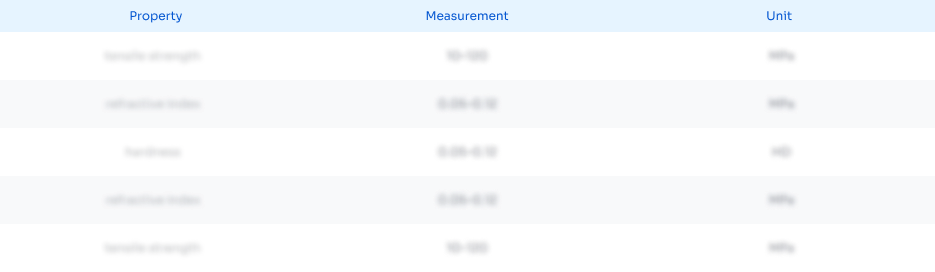
Abstract
Description
Claims
Application Information

- Generate Ideas
- Intellectual Property
- Life Sciences
- Materials
- Tech Scout
- Unparalleled Data Quality
- Higher Quality Content
- 60% Fewer Hallucinations
Browse by: Latest US Patents, China's latest patents, Technical Efficacy Thesaurus, Application Domain, Technology Topic, Popular Technical Reports.
© 2025 PatSnap. All rights reserved.Legal|Privacy policy|Modern Slavery Act Transparency Statement|Sitemap|About US| Contact US: help@patsnap.com