Space general position and orientation measurement standard of machine vision measurement system
A technology of machine vision measurement and system space, which is applied in the direction of measuring devices, instruments, optical devices, etc.
- Summary
- Abstract
- Description
- Claims
- Application Information
AI Technical Summary
Problems solved by technology
Method used
Image
Examples
Embodiment Construction
[0066] Below in conjunction with accompanying drawing, the present invention is described in further detail:
[0067] refer to Figure 1 to Figure 18 , the general position and attitude measurement datum of the machine vision measurement system space is composed of the position adjustment part A and the attitude adjustment part B. The position adjustment part A completes the adjustment of the spatial position, and the posture adjustment part B completes the adjustment of the spatial angle.
[0068] The position adjustment part A includes a bottom plate 1, a longitudinal guide rail 2, a slider 3, a transverse connecting plate 4, a transverse guide rail 5, a cable mounting plate 6, a sensor 7, a sensor mounting frame 8, a sleeve 9, and a vertical base 10 , connecting plate 11, leading screw 12, guide post 13, end cover 14, hand wheel 15, backguy mount 18, L-shaped plate 35, upper bearing 44 and lower bearing 45.
[0069] The bottom plate 1 is a rectangular steel plate, and the ...
PUM
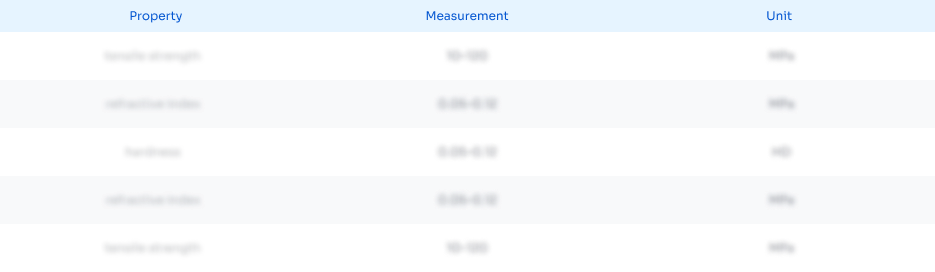
Abstract
Description
Claims
Application Information

- R&D
- Intellectual Property
- Life Sciences
- Materials
- Tech Scout
- Unparalleled Data Quality
- Higher Quality Content
- 60% Fewer Hallucinations
Browse by: Latest US Patents, China's latest patents, Technical Efficacy Thesaurus, Application Domain, Technology Topic, Popular Technical Reports.
© 2025 PatSnap. All rights reserved.Legal|Privacy policy|Modern Slavery Act Transparency Statement|Sitemap|About US| Contact US: help@patsnap.com