Built-in clutch and combined motor with same
A clutch, built-in technology, applied in the direction of clutches, magnetic drive clutches, non-mechanical drive clutches, etc., can solve problems such as unreasonable force structure, troublesome motor assembly, jamming, etc., to improve the torque transmission per unit space and avoid Clutch failure, the effect of ensuring stability
- Summary
- Abstract
- Description
- Claims
- Application Information
AI Technical Summary
Problems solved by technology
Method used
Image
Examples
Embodiment Construction
[0073] Please refer to Figure 1 to Figure 14 As shown, it shows the specific structure of the first embodiment of the present invention, the clutch includes a stationary housing 10 and a clutch assembly that rotates in the housing 10, the clutch assembly includes a driving member 20, a slide block 30, Driven part 40, wherein the driving part 20 is used as a driving wheel, a motor is connected to the reduction box and then connected to the driving part 20, the driven part 40 is used as a driven wheel, the driving part 20 is concentrically connected with the driven part 40, the driving part 20 drives the driven member 40 to rotate through the slide block 30 rotatably adsorbed on the driving member 20. When the clutch is “closed”, the driving member 20, the slide block 30 and the driven member 40 rotate synchronously.
[0074] Among them, such as figure 1 and figure 2 As shown, the housing 10 is cylindrical and includes a housing main body 11 and a cover body 12. The housing ...
PUM
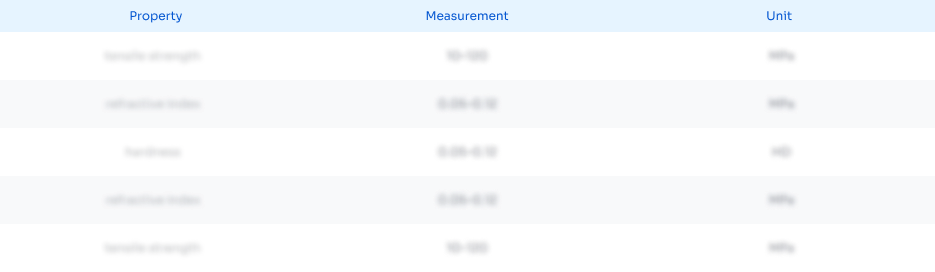
Abstract
Description
Claims
Application Information

- R&D
- Intellectual Property
- Life Sciences
- Materials
- Tech Scout
- Unparalleled Data Quality
- Higher Quality Content
- 60% Fewer Hallucinations
Browse by: Latest US Patents, China's latest patents, Technical Efficacy Thesaurus, Application Domain, Technology Topic, Popular Technical Reports.
© 2025 PatSnap. All rights reserved.Legal|Privacy policy|Modern Slavery Act Transparency Statement|Sitemap|About US| Contact US: help@patsnap.com