Rear fender assembly for small motor vehicles
A technology for rear fenders and motor vehicles, which is applied in the directions of fenders, bicycle accessories, transportation and packaging, etc., can solve the problems of unchanged operation, complicated and inconvenient rear fenders, etc., and achieves improved strength and rigidity. Improve maintainability and ensure neutrality
- Summary
- Abstract
- Description
- Claims
- Application Information
AI Technical Summary
Problems solved by technology
Method used
Image
Examples
Embodiment Construction
[0020] refer to Figure 1~Figure 4 , the rear fender assembly of the small motor vehicle of the present invention, it comprises the rear fender 2 that is installed on the vehicle frame 1, and described rear fender 2 is arch-like structure for adapting rear wheel, also includes Tailgate support 3, the tailgate support 3 is a J-shaped structure, the tailgate support 3 is preferably a stamping part, the vertical direction part 31 of the tailgate support 3 is parallel to the vehicle width center plane and is located at the two ends of the rear fender 2 top. side, wherein the center plane of the vehicle width is the plane of symmetry of the locomotive body width, and the horizontal direction part 32 extending from the bottom end of the vertical direction part 31 is adapted to the direction along the wall of the top of the rear fender 2, that is, the horizontal direction part of the tailgate bracket 3 Designed to follow the shape of the outer periphery of the rear fender 2, the end ...
PUM
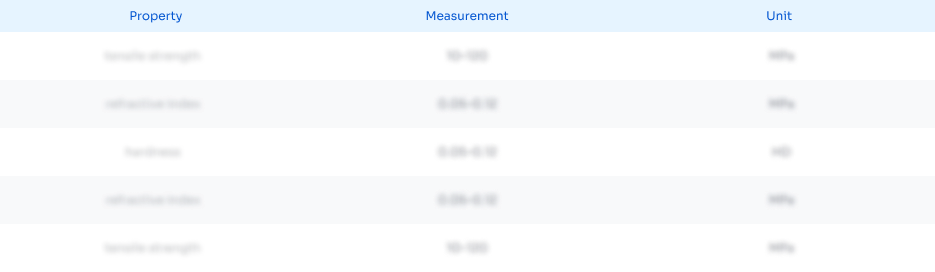
Abstract
Description
Claims
Application Information

- Generate Ideas
- Intellectual Property
- Life Sciences
- Materials
- Tech Scout
- Unparalleled Data Quality
- Higher Quality Content
- 60% Fewer Hallucinations
Browse by: Latest US Patents, China's latest patents, Technical Efficacy Thesaurus, Application Domain, Technology Topic, Popular Technical Reports.
© 2025 PatSnap. All rights reserved.Legal|Privacy policy|Modern Slavery Act Transparency Statement|Sitemap|About US| Contact US: help@patsnap.com