A Predictive Control Method for Complex Digital Control System
A digital control system and predictive control technology, applied in digital control, electrical program control, etc., can solve the problems of reduced prediction accuracy, low prediction accuracy, and long iterative calculation time, so as to solve the problem of sampling error, improve the search speed, The effect of reducing the time required
- Summary
- Abstract
- Description
- Claims
- Application Information
AI Technical Summary
Problems solved by technology
Method used
Image
Examples
Embodiment Construction
[0029] The preferred embodiments of the present invention will be further described below in conjunction with the accompanying drawings.
[0030] Such as figure 1 , figure 2 , image 3 , Figure 4 shown. The superconducting magnetic energy storage system solves a series of output power fluctuations including distributed power generation, power peak regulation, frequency offset, high-order harmonic suppression, voltage drop, Power system problems such as voltage surges. Since the dynamic power exchange requirements of the external DC or AC system change dynamically, it can be equivalent to a DC load resistance with constant rated voltage but dynamic change of its own resistance during the discharge process of the superconducting magnet. Take load resistance controlled constant voltage discharge control application as an example.
[0031] Superconducting magnet controlled constant voltage discharge control system (system block diagram as figure 2 Shown) consists of the ...
PUM
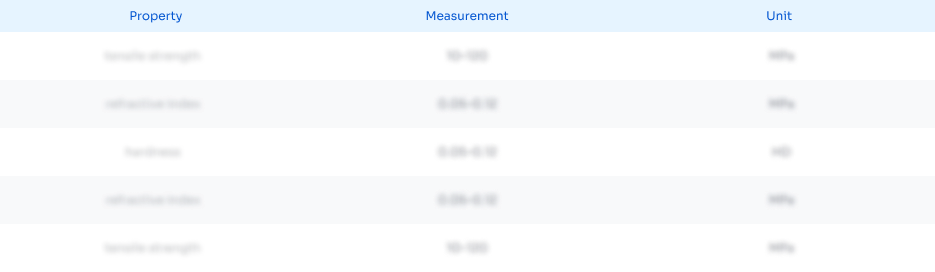
Abstract
Description
Claims
Application Information

- R&D
- Intellectual Property
- Life Sciences
- Materials
- Tech Scout
- Unparalleled Data Quality
- Higher Quality Content
- 60% Fewer Hallucinations
Browse by: Latest US Patents, China's latest patents, Technical Efficacy Thesaurus, Application Domain, Technology Topic, Popular Technical Reports.
© 2025 PatSnap. All rights reserved.Legal|Privacy policy|Modern Slavery Act Transparency Statement|Sitemap|About US| Contact US: help@patsnap.com