Rotary hearth furnace
A technology of rotary hearth furnace and furnace body, which is applied in the direction of furnace, hearth type furnace, furnace type, etc., and can solve the problems of low production efficiency of rotary hearth furnace process, uneven radiation heat transfer of material layer, low metallization rate, etc. Achieve the effect of improving heat transfer efficiency, improving heat transfer efficiency, and uniform heating
- Summary
- Abstract
- Description
- Claims
- Application Information
AI Technical Summary
Problems solved by technology
Method used
Image
Examples
Embodiment Construction
[0024] The specific implementation manners of the present invention will be described in detail below in conjunction with the accompanying drawings.
[0025] Such as figure 1 Shown is a schematic structural view of an embodiment of the rotary hearth furnace of the present invention. The rotary hearth furnace of this embodiment includes a furnace body 1 and at least one material layer stirring device fixedly arranged in the furnace body and above the rotating platform. The furnace body 1 is provided with a rotating platform 2 and is used to drive the rotating platform. 2. The driving mechanism for rotation. A supporting device 3 for supporting the rotating platform is provided under the rotating platform 2. The material layer stirring device includes at least one row of agitating rake teeth 4 extending toward the rotating platform 2 and used to stir the material layer placed on the rotating platform. . There are at least three material bed agitating devices in this embodiment...
PUM
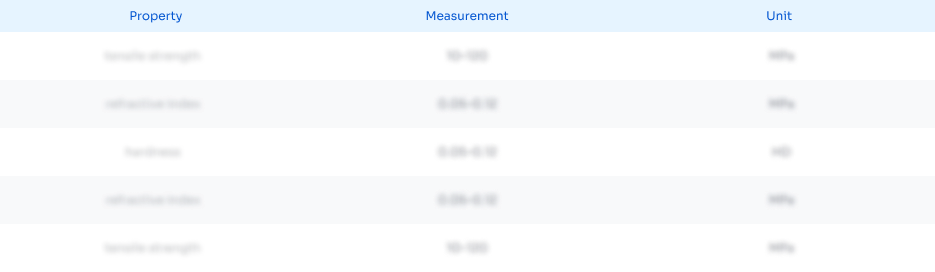
Abstract
Description
Claims
Application Information

- R&D
- Intellectual Property
- Life Sciences
- Materials
- Tech Scout
- Unparalleled Data Quality
- Higher Quality Content
- 60% Fewer Hallucinations
Browse by: Latest US Patents, China's latest patents, Technical Efficacy Thesaurus, Application Domain, Technology Topic, Popular Technical Reports.
© 2025 PatSnap. All rights reserved.Legal|Privacy policy|Modern Slavery Act Transparency Statement|Sitemap|About US| Contact US: help@patsnap.com