Manufacture process of shell fabric with memory function
A production process and function technology, applied in the direction of dry cleaning fiber products, textiles, fabrics, etc., can solve the problems of cumbersome production process, fabric crepe, high production cost, and achieve the effect of strong memory function and soft hand feeling.
- Summary
- Abstract
- Description
- Claims
- Application Information
AI Technical Summary
Problems solved by technology
Method used
Examples
Embodiment 1
[0015] Embodiment 1, the manufacturing process of the fabric with memory function is carried out according to the following steps:
[0016] 1) 50D, the total number of yarns is 281T, the warp density is 205T, and the weft density is 76T for distributing;
[0017] 2) Continuous retreat at a speed of 30-60 yards per minute, and the temperature is 90-100 0 C;
[0018] 3) Desizing: Add the following additives per liter of water during the desizing process. The steps are: first heat the water temperature to 30-40 0 C. Add 1g of refining agent at a uniform speed within 5-8 minutes; add 1g of degreasing agent at a uniform speed within 3-5 minutes; 0 Keep it under the temperature condition of C for 30-60 minutes;
[0019] 4) Dyeing: Add the following additives per liter of water during the dyeing process, the steps are: first heat the water temperature to 30-40 0 C. Add 0.3g of chelating agent at a uniform speed within 3-5 minutes; add 1g of dispersing and leveling agent at a ...
Embodiment 2
[0025] Embodiment 2, the manufacturing process of the fabric with memory function is carried out according to the following steps:
[0026] 1) 50D, the total number of yarns is 281T, the warp density is 205T, and the weft density is 76T for distributing;
[0027] 2) Continuous retreat at a speed of 30-60 yards per minute, and the temperature is 90-100 0 C;
[0028] 3) Desizing: Add the following additives per liter of water during the desizing process. The steps are: first heat the water temperature to 30-40 0 C. Add 3g of refining agent at a uniform speed within 5-8 minutes; add 2g of degreasing agent at a uniform speed within 3-5 minutes; 0 Keep it under the temperature condition of C for 30-60 minutes;
[0029] 4) Dyeing: Add the following additives per liter of water during the dyeing process, the steps are: first heat the water temperature to 30-40 0 C, add 0.7g of chelating agent at a uniform speed within 3-5 minutes; add 2g of dispersing and leveling agent at a ...
Embodiment 3
[0035] Embodiment 3, the manufacturing process of fabric with memory function, is carried out according to the following steps:
[0036] 1) 50D, the total number of yarns is 281T, the warp density is 205T, and the weft density is 76T for distributing;
[0037] 2) Continuous retreat at a speed of 30-60 yards per minute, and the temperature is 90-100 0 C;
[0038] 3) Desizing: Add the following additives per liter of water during the desizing process. The steps are: first heat the water temperature to 30-40 0 C. Add 4g of refining agent at a uniform speed within 5-8 minutes; add 3g of degreasing agent at a uniform speed within 3-5 minutes; 0 Keep it under the temperature condition of C for 30-60 minutes;
[0039] 4) Dyeing: Add the following additives per liter of water during the dyeing process, the steps are: first heat the water temperature to 30-40 0 C. Add 1 g of chelating agent at a uniform speed within 3-5 minutes; add 2.5 g of dispersing and leveling agent at a u...
PUM
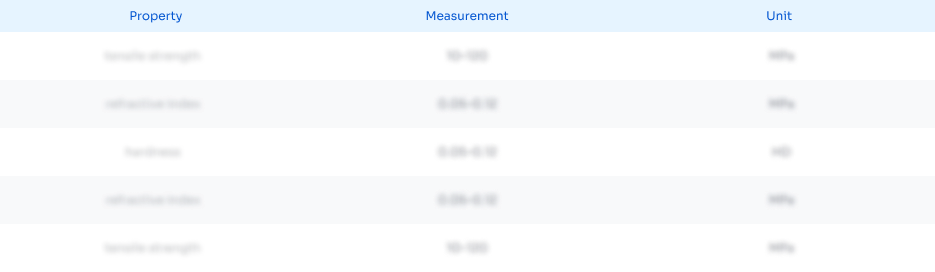
Abstract
Description
Claims
Application Information

- R&D
- Intellectual Property
- Life Sciences
- Materials
- Tech Scout
- Unparalleled Data Quality
- Higher Quality Content
- 60% Fewer Hallucinations
Browse by: Latest US Patents, China's latest patents, Technical Efficacy Thesaurus, Application Domain, Technology Topic, Popular Technical Reports.
© 2025 PatSnap. All rights reserved.Legal|Privacy policy|Modern Slavery Act Transparency Statement|Sitemap|About US| Contact US: help@patsnap.com