Plate production method by hot continuous rolling
A production method and hot continuous rolling technology, applied in the direction of rolling, metal rolling, metal rolling, etc., can solve the problems of increasing labor intensity of workers and the impact of rolling mill operation rate, and achieve the effect of reducing labor intensity and improving production capacity.
- Summary
- Abstract
- Description
- Claims
- Application Information
AI Technical Summary
Problems solved by technology
Method used
Examples
Embodiment 1
[0037] Raw material end face specification size: 160mm×1250mm
[0038] Steel type: Q235B
[0039] Checkered plate product specifications and sizes are: 5.5mm × 1250mm
[0040] The temperature of each section of finish rolling: the entrance of finish rolling is 1040~1070°C; the finish rolling is 940~970°C.
[0041] F1~F5 finish rolling work roll configuration before finished roll is shown in Table 2 above, F6 work roll crown is -0.14~0mm.
[0042] The range of parameters such as the reduction distribution rate of the corresponding checkered plate product 5.5mm×1250mm is shown in Table 3.
[0043] Table 3 Checkered plate products 5.5mm×1250mm (middle billet thickness: 34~35mm)
[0044] project
Embodiment 2
[0046] Raw material end face specification size: 160mm×1250mm
[0047] Steel type: Q235B
[0048] Checkered plate product specifications and sizes are: 6.0mm × 1250mm
[0049] The temperature of each section of finish rolling: the entrance of finish rolling is 1040~1070°C; the finish rolling is 940~970°C.
[0050] F1~F5 finish rolling work roll configuration before finished roll is shown in Table 2 above, F6 work roll crown is -0.14~0mm.
[0051] The range of parameters such as the reduction distribution rate of the corresponding checkered plate product 6.0mm×1250mm is shown in Table 4.
[0052] Table 4 checkered plate products 6.0mm×1250mm (middle billet thickness: 34~35mm)
[0053] project
Embodiment 3
[0055] Raw material end face specification size: 160mm×1250mm
[0056] Steel type: Q235B
[0057] Flat product specifications and sizes are: 6.0mm×1250mm
[0058] The temperature of each section of finish rolling: the entrance of finish rolling is 1040~1070°C; the finish rolling is 940~970°C.
[0059] The profile configuration of the finished work rolls of F1~F5 is shown in Table 2 above, and the crown of the work rolls of F6 is -0.18~-0.1mm.
[0060] See Table 5 for the range of parameters such as the reduction distribution ratio of the corresponding flat product 6.0mm×1250mm.
[0061] Table 5 Flat product 6.0mm×1250mm (middle billet thickness: 34~35mm)
[0062] project
F1
F2
F3
F4
F5
F6
Speed (m / s)
1.1
1.7
2.3
2.81
3.5
4.61
35~40
31~34
24~28
23~27
21~24
11~14
Rolling force budget (t)
1400~1600
1300~1500
...
PUM
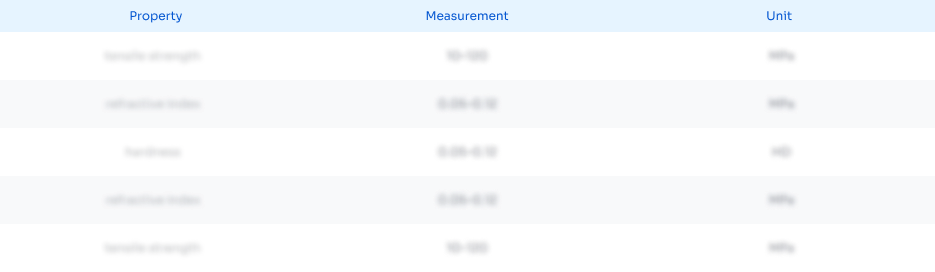
Abstract
Description
Claims
Application Information

- Generate Ideas
- Intellectual Property
- Life Sciences
- Materials
- Tech Scout
- Unparalleled Data Quality
- Higher Quality Content
- 60% Fewer Hallucinations
Browse by: Latest US Patents, China's latest patents, Technical Efficacy Thesaurus, Application Domain, Technology Topic, Popular Technical Reports.
© 2025 PatSnap. All rights reserved.Legal|Privacy policy|Modern Slavery Act Transparency Statement|Sitemap|About US| Contact US: help@patsnap.com