Special forming mold for T-shaped precast beam plate
A technology for forming molds and prefabricated beams, applied in the direction of molds, mold separation devices, etc., can solve the problems of inability to ensure that the templates are exactly the same, low production efficiency, and low efficiency, so as to avoid repeated disassembly and assembly of templates, save labor and materials, and improve The effect of work efficiency
- Summary
- Abstract
- Description
- Claims
- Application Information
AI Technical Summary
Problems solved by technology
Method used
Image
Examples
Embodiment 1
[0011] Embodiment 1: refer to Figure 1~3 . A special forming mold for T-shaped prefabricated beam slabs, including a base 4, on which is provided a T-shaped formwork for making T-shaped prefabricated beams and slabs, the T-shaped formwork consists of two sets of side formworks 2 and two sets of end formworks 1, two sets of side formworks 2 are placed symmetrically on the left and right sides of the upper end of the base 4, the two sets of end formworks 1 are respectively connected to the front and rear ends of the two sets of side formworks 2, and the base 4 is provided with a number of side formworks 2 convenient for both sides As well as two sets of guide rails 4a for the outward sliding of the end formwork 1, the lower ends of the side formwork 2 and the lower ends of the end formwork 1 are respectively provided with guide grooves that match and connect with the guide rails 4a, that is, the side formwork 2 and the end formwork 1 are respectively along the guide rails at th...
Embodiment 2
[0012] Embodiment 2: refer to Figure 1~3 . After using this mold, the same production line only needs to be equipped with a part-time mechanical operator, and at least 60 sets of templates can be assembled a day, which not only saves labor, but also greatly improves work efficiency; , resulting in large errors in the angle and size of the beams and slabs; the possibility of manual constraints on the mass production process is also reduced.
[0013] In this set of molds, after the initial setting of the concrete, the side formwork and end formwork are opened, and then covered with thermal insulation tarpaulin for steam curing. After 72 hours, the prefabricated beam slab can be removed from the base.
PUM
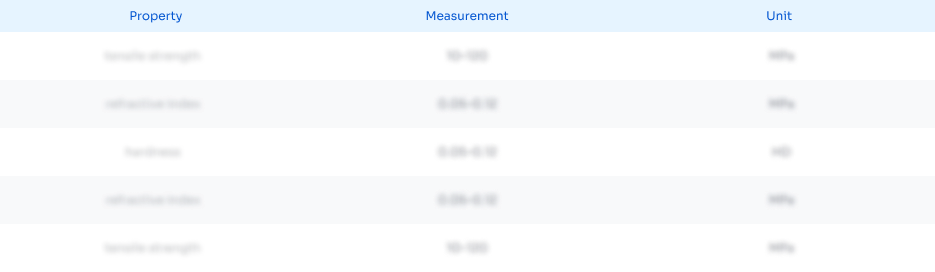
Abstract
Description
Claims
Application Information

- Generate Ideas
- Intellectual Property
- Life Sciences
- Materials
- Tech Scout
- Unparalleled Data Quality
- Higher Quality Content
- 60% Fewer Hallucinations
Browse by: Latest US Patents, China's latest patents, Technical Efficacy Thesaurus, Application Domain, Technology Topic, Popular Technical Reports.
© 2025 PatSnap. All rights reserved.Legal|Privacy policy|Modern Slavery Act Transparency Statement|Sitemap|About US| Contact US: help@patsnap.com