Yarn foam sizing process and device
A foam sizing and yarn technology, applied in the field of textile sizing, can solve the problems of sizing consumption, desizing wastewater pollution, and high sizing permeability, and achieve the effects of improving wear resistance and low operating costs
- Summary
- Abstract
- Description
- Claims
- Application Information
AI Technical Summary
Problems solved by technology
Method used
Image
Examples
Embodiment 1
[0016] Example 1: The sizing of A04044-1202651-1L (yarn count: pure cotton 80 pounds, total warp number: 8060) yarn, the specific operation steps are:
[0017] Preparation of slurry: mix polyvinyl alcohol, modified starch, acrylic acid and water at a mass ratio of 2:6:2:200 to make a mixture, and then add a foaming agent, the volume ratio of the foaming agent to the above mixture The ratio is 1:100, mix evenly to make a slurry;
[0018] Slurry treatment: heat the above slurry to 90°C first, then cool it down to 40°C, and then add it to the foamer.
[0019] Yarn sizing: the pressure between the two pressure rollers 4 in the size tank 3 is 12000N, and the foam generated by the foamer 1 sprays down from the nozzle 5 of the foam applicator 2 onto the two oppositely rotating pressure rollers 4 In the middle, the yarn is first soaked in the foam slurry in the size tank 3, and then passes through the middle of the two pressure rollers 4 from the bottom, so that when the yarn passes ...
Embodiment 2
[0020] Example 2: The sizing of Q04041-1200625-3L (yarn count: pure cotton 40 pounds, total warp number: 8032) yarn, the specific operation steps are:
[0021] Preparation of slurry: mix polyvinyl alcohol, modified starch, acrylic acid and water at a mass ratio of 5:16:4:300 to make a mixture, and then add a foaming agent, the volume ratio of the foaming agent to the above mixture 2:100, mix evenly to make a slurry;
[0022] Slurry treatment: heat the above slurry to 110°C first, then lower the temperature to 50°C, and then add it to the foamer.
[0023] Yarn sizing: the pressure between the two pressure rollers 4 in the size tank 3 is 14000N, and the foam generated by the foamer 1 sprays down from the nozzle 5 of the foam applicator 2 onto the two oppositely rotating pressure rollers 4 In the middle, the yarn passes through the middle of the two squeeze rollers 4 from the bottom, so that when the yarn passes through the squeeze rollers 4, it is moderately squeezed by the squ...
Embodiment 3
[0024] Example 3: The sizing of A04041-1214149-1L (yarn count: pure cotton 30 pounds, total warp number: 8020) yarn, the specific operation steps are:
[0025] Preparation of slurry: mix polyvinyl alcohol, modified starch, acrylic acid and water at a mass ratio of 5:10:5:200 to make a mixture, and then add a foaming agent, the volume ratio of the foaming agent to the above mixture 3:100, mix evenly to make a slurry;
[0026] Slurry treatment: heat the above slurry to 120°C first, then cool it down to 60°C, and then add it to the foamer.
[0027] Yarn sizing: the pressure between the two pressure rollers 4 in the size tank 3 is 18000N, and the foam generated by the foamer 1 sprays down from the nozzle 5 of the foam applicator 2 onto the two oppositely rotating pressure rollers 4 In the middle, the yarn passes through the middle of the two squeeze rollers 4 from the bottom, so that when the yarn passes through the squeeze rollers 4, it is moderately squeezed by the squeeze roll...
PUM
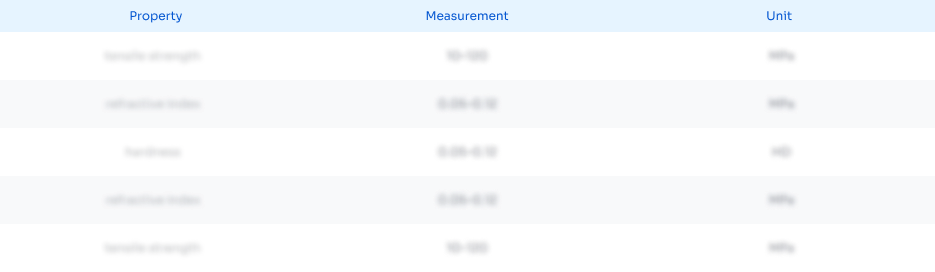
Abstract
Description
Claims
Application Information

- R&D
- Intellectual Property
- Life Sciences
- Materials
- Tech Scout
- Unparalleled Data Quality
- Higher Quality Content
- 60% Fewer Hallucinations
Browse by: Latest US Patents, China's latest patents, Technical Efficacy Thesaurus, Application Domain, Technology Topic, Popular Technical Reports.
© 2025 PatSnap. All rights reserved.Legal|Privacy policy|Modern Slavery Act Transparency Statement|Sitemap|About US| Contact US: help@patsnap.com