Preparation method of high purity N,N'-dicyclohexylthiourea
A dicyclohexylthiourea, high-purity technology, applied in the direction of organic chemistry, can solve the problems of inapplicability to industrial production, easy loss of solvent, cumbersome operation, etc., and achieve the effect of saving cost, reducing energy consumption and ensuring removal efficiency
- Summary
- Abstract
- Description
- Claims
- Application Information
AI Technical Summary
Problems solved by technology
Method used
Image
Examples
Embodiment 1
[0015] Add 500kg of solvent water and 200kg of cyclohexylamine to the reaction kettle, start stirring, raise the temperature to 25°C, start to add 82 kg of carbon disulfide dropwise, control the dropping time for 2h, and control the temperature at 25-30°C; Insulate at -30°C for 1 hour, filter after the reaction is complete, collect the filtered intermediate salt solid and put it back into the reaction kettle, open the vacuum valve, keep the vacuum negative pressure at -0.05MPa, and raise the temperature to 90 o C was dried for 3 hours to remove hydrogen sulfide to obtain 241 kg of N, N'-dicyclohexylthiourea product with a yield of 99.14% and a purity of 99.68%.
[0016] The obtained mother liquor is reused in the following 10 reaction cycles without any treatment, and an average of 241.55 kg of product can be obtained, with a yield of 99.36%.
[0017] Mother liquor cycle times Product weight / kg Product yield / % purity / % 0 241 99.14 99.68 1 241 99.14 ...
Embodiment 2
[0019] Add 500kg of solvent water and 200kg of cyclohexylamine to the reaction kettle, start stirring, cool down to 10°C, start to add 80 kg of carbon disulfide dropwise, control the dropping time for 3 hours, and control the temperature at 10-15°C; Insulate at -15°C for 1h, filter after the reaction is complete, collect the filtered intermediate salt solid and put it back into the reaction kettle, open the vacuum valve, keep the vacuum negative pressure at -0.03MPa, and raise the temperature to 60 o C was dried for 5 hours to remove hydrogen sulfide to obtain 240.3 kg of N, N'-dicyclohexylthiourea product with a yield of 99.08% and a purity of 99.56%.
Embodiment 3
[0021] Add 500kg of solvent water and 160kg of cyclohexylamine to the reaction kettle, start stirring, raise the temperature to 30°C, start to add 68 kg of carbon disulfide dropwise, control the dropping time for 1.5h, and control the temperature at 30-40°C; Insulate at 25-30°C for 2 hours, filter after the reaction is completed, collect the filtered intermediate salt solid and put it back into the reactor, open the vacuum valve, keep the vacuum negative pressure at -0.07MPa, and raise the temperature to 80 o C was dried for 2 hours to remove hydrogen sulfide to obtain 192.3 kg of N,N'-dicyclohexylthiourea product with a yield of 99.08% and a purity of 99.56%.
PUM
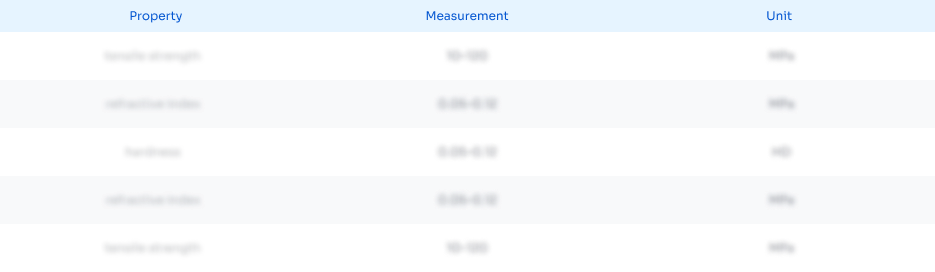
Abstract
Description
Claims
Application Information

- R&D
- Intellectual Property
- Life Sciences
- Materials
- Tech Scout
- Unparalleled Data Quality
- Higher Quality Content
- 60% Fewer Hallucinations
Browse by: Latest US Patents, China's latest patents, Technical Efficacy Thesaurus, Application Domain, Technology Topic, Popular Technical Reports.
© 2025 PatSnap. All rights reserved.Legal|Privacy policy|Modern Slavery Act Transparency Statement|Sitemap|About US| Contact US: help@patsnap.com