Optimal control system and method for realizing instant excavation turning angle and excavation force of bucket
A technology for optimizing control and digging force, applied to mechanically driven excavators/dredgers, etc., can solve problems such as adverse effects of bucket excavation full load, unfavorable soil cutting, lifting, etc., to improve excavation efficiency, reduce loss, expand The effect of mining range
- Summary
- Abstract
- Description
- Claims
- Application Information
AI Technical Summary
Problems solved by technology
Method used
Image
Examples
Embodiment Construction
[0031] The present invention will be further described below in combination with principle diagrams and specific operation examples.
[0032] Such as figure 1 and image 3 As shown in a, the present invention realizes the optimal control system of bucket instantaneous digging angle and digging force, including connecting rod cylinder a4, laser locator 6, boom cylinder stroke displacement sensor s1, stick cylinder stroke displacement sensor s2, bucket cylinder stroke Displacement sensor s3, connecting rod cylinder stroke displacement sensor s4, boom cylinder pressure sensor p1, stick cylinder pressure sensor p2, bucket cylinder pressure sensor p3, connecting rod cylinder pressure sensor p4, programmable controller 7 and control connecting rod cylinder The electro-hydraulic proportional valve 8 for oil quantity, the signal output terminals of all the above sensors are respectively connected with the programmable controller 7, and the output terminals of the programmable control...
PUM
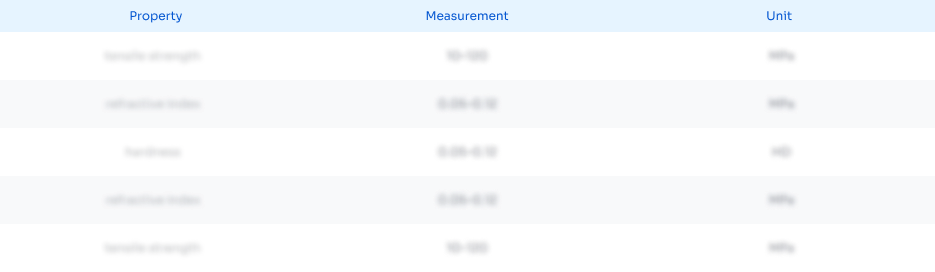
Abstract
Description
Claims
Application Information

- R&D Engineer
- R&D Manager
- IP Professional
- Industry Leading Data Capabilities
- Powerful AI technology
- Patent DNA Extraction
Browse by: Latest US Patents, China's latest patents, Technical Efficacy Thesaurus, Application Domain, Technology Topic, Popular Technical Reports.
© 2024 PatSnap. All rights reserved.Legal|Privacy policy|Modern Slavery Act Transparency Statement|Sitemap|About US| Contact US: help@patsnap.com