Lead spot welding tooling and line spot welding method for sound films of loudspeakers
A speaker and sound film technology, applied in the field of speaker sound film point and line tooling, can solve problems such as the inability of the speaker to produce sound, the quality of the speaker and the pure sound of the speaker, etc., to avoid fatigue disconnection, improve sound quality, and reduce the overall load. Effect
- Summary
- Abstract
- Description
- Claims
- Application Information
AI Technical Summary
Problems solved by technology
Method used
Image
Examples
Embodiment Construction
[0025] The present invention will be further described below in conjunction with the accompanying drawings and specific embodiments.
[0026] see figure 1 , 2 , loudspeaker sound film dot line tooling, which includes a lower base 1, an upper pressure seat 2 arranged on the lower base 1 and matched with the lower base; the upper end surface of the lower base 1 is provided with two upwardly protruding arc limit ribs 3 , 301, there are two arc-shaped limit ribs, the limit surfaces 4 and 401 of the two arc-shaped limit ribs are on the same circle, and there is a gap between the two arc-shaped limit ribs 5. It is easy to take and place the pot frame 6, and when the circular pot frame 6 is placed on the lower base 1, it is limited by two arc-shaped limit ribs 3, 301, so that the pot frame cannot be left and right , move back and forth; clamping notches 16, 161 are set on one of the arc-shaped limit ribs 3; in the middle of the upper end surface of the lower base 1, an upwardly rai...
PUM
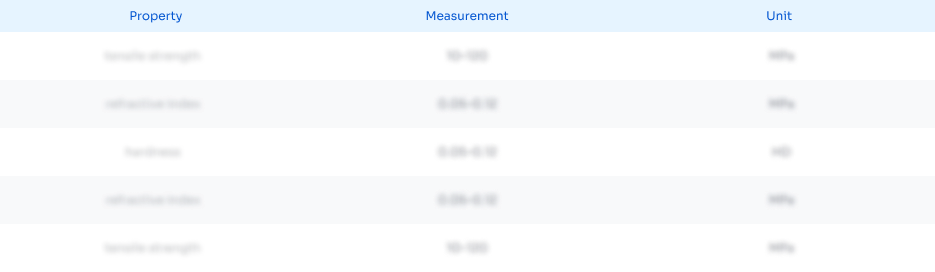
Abstract
Description
Claims
Application Information

- R&D Engineer
- R&D Manager
- IP Professional
- Industry Leading Data Capabilities
- Powerful AI technology
- Patent DNA Extraction
Browse by: Latest US Patents, China's latest patents, Technical Efficacy Thesaurus, Application Domain, Technology Topic, Popular Technical Reports.
© 2024 PatSnap. All rights reserved.Legal|Privacy policy|Modern Slavery Act Transparency Statement|Sitemap|About US| Contact US: help@patsnap.com