Biomass briquetting machine
A biomass molding machine and machine base technology, which is applied to material molding presses, presses, manufacturing tools, etc., can solve the problems of mold wear, increase power consumption, affect assembly progress, etc., and reduce mold wear. , the effect of reducing safety accidents and enhancing adaptability
- Summary
- Abstract
- Description
- Claims
- Application Information
AI Technical Summary
Problems solved by technology
Method used
Image
Examples
Embodiment 1
[0086] A biomass forming machine, comprising a machine base 1, a power transmission device 2, a main shaft 3, a feeding device, a pressure roller mechanism and an annular molding die, the feeding device includes a feeding power transmission device 4, a feeding bin 5, Feed inlet 6, discharge port 8 and screw conveyor rod 7, described feeding power transmission device 4 is positioned at the side of feeding bin 5, and feeding inlet 6 is positioned at the top of feeding bin 5 and is close to one end of power transmission device 4, and discharging The port 8 is located at the bottom of the feeding bin 5 and away from the end of the feeding power transmission device 4, the screw conveying rod 7 is located in the feeding bin 5 and connected with the feeding power transmission device 4, the machine base 1 is located below the discharge port 8, and the main shaft 3 is vertically Through the machine base 1, the lower end of the main shaft 3 is connected with the power transmission device...
Embodiment 2
[0088] A biomass forming machine, comprising a machine base 1, a power transmission device 2, a main shaft 3, a feeding device, a pressure roller mechanism and an annular molding die, the feeding device includes a feeding power transmission device 4, a feeding bin 5, Feed inlet 6, discharge port 8 and screw conveyor rod 7, described feeding power transmission device 4 is positioned at the side of feeding bin 5, and feeding inlet 6 is positioned at the top of feeding bin 5 and is close to one end of power transmission device 4, and discharging The port 8 is located at the bottom of the feeding bin 5 and away from the end of the feeding power transmission device 4, the screw conveying rod 7 is located in the feeding bin 5 and connected with the feeding power transmission device 4, the machine base 1 is located below the discharge port 8, and the main shaft 3 is vertically Through the machine base 1, the lower end of the main shaft 3 is connected with the power transmission device...
Embodiment 3
[0090]A biomass forming machine, comprising a machine base 1, a power transmission device 2, a main shaft 3, a feeding device, a pressure roller mechanism and an annular molding die, the feeding device includes a feeding power transmission device 4, a feeding bin 5, Feed inlet 6, discharge port 8 and screw conveyor rod 7, described feeding power transmission device 4 is positioned at the side of feeding bin 5, and feeding inlet 6 is positioned at the top of feeding bin 5 and is close to one end of power transmission device 4, and discharging The port 8 is located at the bottom of the feeding bin 5 and away from the end of the feeding power transmission device 4, the screw conveying rod 7 is located in the feeding bin 5 and connected with the feeding power transmission device 4, the machine base 1 is located below the discharge port 8, and the main shaft 3 is vertically Through the machine base 1, the lower end of the main shaft 3 is connected with the power transmission device ...
PUM
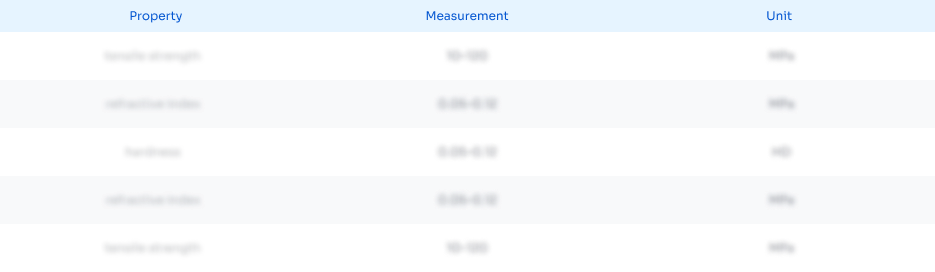
Abstract
Description
Claims
Application Information

- R&D Engineer
- R&D Manager
- IP Professional
- Industry Leading Data Capabilities
- Powerful AI technology
- Patent DNA Extraction
Browse by: Latest US Patents, China's latest patents, Technical Efficacy Thesaurus, Application Domain, Technology Topic, Popular Technical Reports.
© 2024 PatSnap. All rights reserved.Legal|Privacy policy|Modern Slavery Act Transparency Statement|Sitemap|About US| Contact US: help@patsnap.com