Magnetic suspension molecular pump rotor floating position selection method and rotor floating control method
A magnetic levitation and molecular pump technology, applied in pump control, non-variable pumps, machines/engines, etc., to achieve stable working characteristics and stable floating effects
- Summary
- Abstract
- Description
- Claims
- Application Information
AI Technical Summary
Problems solved by technology
Method used
Image
Examples
Embodiment 1
[0041] This embodiment provides a method for selecting the floating position of the rotor of a magnetic levitation molecular pump, which includes the following steps:
[0042] I. Establish a Cartesian coordinate system with the center of the inner circle of the radial protective bearing stator as the origin, and divide the inner circle of the radial protective bearing stator into n sectoral intervals on average (n is a natural number and n≥4);
[0043] II. Obtaining the float control parameters of the rotor and the float characteristic parameters of the rotor when the rotors are respectively located in the n intervals through a levitation test;
[0044] III. Comparing the floating characteristic parameters when the rotors are respectively located in the n intervals, selecting the optimal interval suitable for the floating of the rotor, and outputting the X direction output of the corresponding radial displacement sensor when the rotor is located in the optimal interval The sig...
Embodiment 2
[0057] In this embodiment, on the basis of Embodiment 1, further, the step II further includes acquiring the float control parameters of the rotor and the float control parameters of the rotor when the rotor is located at multiple positions in the preferred interval. The steps of floating characteristic parameters;
[0058] The step III also includes comparing the float control parameters of the rotor and the float characteristic parameters of the rotor when the rotor is located in multiple positions in the preferred interval, and obtaining the float characteristics of the rotor in the optimal interval The best preferred position, when the rotor is at the preferred position, the corresponding X-direction output signal voltage amplitude, Y-direction output signal voltage amplitude and rotor float control parameters of the corresponding radial displacement sensor are stored in the controller 2 steps in the storage medium within.
[0059] Correspondingly, in the rotor float cont...
PUM
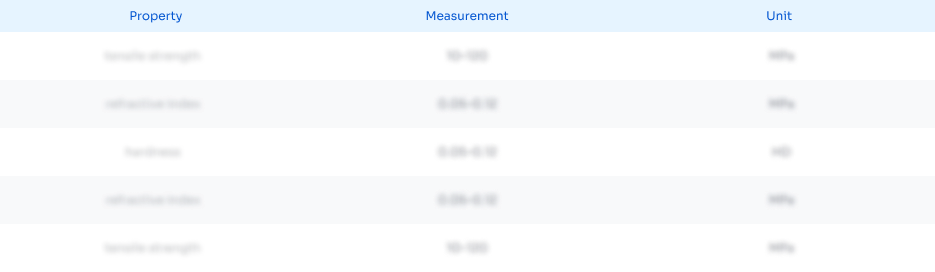
Abstract
Description
Claims
Application Information

- Generate Ideas
- Intellectual Property
- Life Sciences
- Materials
- Tech Scout
- Unparalleled Data Quality
- Higher Quality Content
- 60% Fewer Hallucinations
Browse by: Latest US Patents, China's latest patents, Technical Efficacy Thesaurus, Application Domain, Technology Topic, Popular Technical Reports.
© 2025 PatSnap. All rights reserved.Legal|Privacy policy|Modern Slavery Act Transparency Statement|Sitemap|About US| Contact US: help@patsnap.com