Force application element for fixing in or on fiber-plastic composite component
A technology of force components and composite components, applied in the field of force transmission components, can solve the problems of high mold costs and equipment costs, achieve good connection quality and reduce manufacturing costs
- Summary
- Abstract
- Description
- Claims
- Application Information
AI Technical Summary
Problems solved by technology
Method used
Image
Examples
Embodiment Construction
[0016] figure 1 The structural part 2 shown in includes a first FKV part 2a and a second FKV part 2b, said first and second FKV parts being made, for example, of CFK. A force transmission point is realized in this structural component 2 with the force transmission element 1 .
[0017] The force transmission element 1 is designed as a hybrid component and comprises a metal insert 3 made of steel, which is designed in the form of a sleeve in the force transmission direction F with the formation of a through-hole 9 . The metal insert 3 is enveloped in the shape of a shell by a structure 4 of BMC material, which has a substantially biconical cross-section.
[0018] A contact surface 5 for bearing against the FKV component 2 a and a contact surface 6 for abutting against the FKV component 2 b are each formed by means of the biconical end faces. Furthermore, the contact surfaces 5 and 6 transition into flanges 4a and 4b, respectively, which engage in openings 10a and 10b in the tw...
PUM
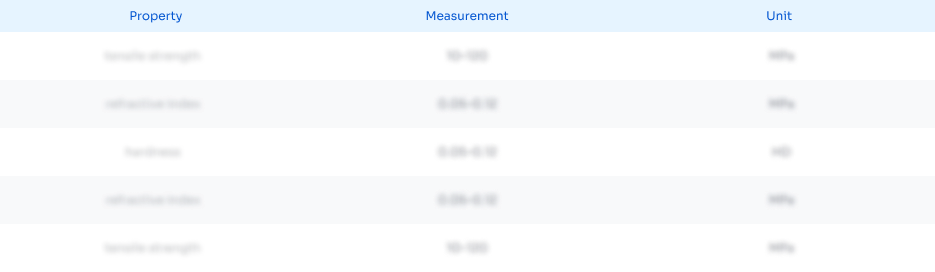
Abstract
Description
Claims
Application Information

- R&D
- Intellectual Property
- Life Sciences
- Materials
- Tech Scout
- Unparalleled Data Quality
- Higher Quality Content
- 60% Fewer Hallucinations
Browse by: Latest US Patents, China's latest patents, Technical Efficacy Thesaurus, Application Domain, Technology Topic, Popular Technical Reports.
© 2025 PatSnap. All rights reserved.Legal|Privacy policy|Modern Slavery Act Transparency Statement|Sitemap|About US| Contact US: help@patsnap.com