Leadless radiation-proof organic glass and preparation method thereof
A plexiglass, radiation protection technology, applied in shielding, nuclear engineering, reactors, etc., can solve problems such as environmental pollution, lead harms human health, etc.
- Summary
- Abstract
- Description
- Claims
- Application Information
AI Technical Summary
Problems solved by technology
Method used
Image
Examples
preparation example Construction
[0023] Preparation of rare earth salts:
[0024] 1. Samarium methacrylate (Sm (MAA) 3 ) preparation
[0025] (1) Sm(OH) 3 Synthesis
[0026] Measure 48mL of concentrated HCl into a 250mL beaker, add 100mL of deionized water to dilute, place on a heating stirrer and heat to about 50°C while stirring, and 27gSm 2 o 3 (Ganzhou Ansheng Inorganic Materials Service Center) Slowly add to the beaker, stir until the solution is colorless and transparent, stop heating, filter the solution to remove insoluble impurities, then slowly add ammonia water, a large amount of precipitation gradually appears, adjust the pH to 8. Suction filtration, washing, and suction filtration of the product were repeated three times until the ammonia smell disappeared, and the precipitate was dried at 110°C to a constant mass to obtain a block of Sm(OH) 3 , take out the dry matter, pulverize it with a high-speed pulverizer, and obtain powdered Sm(OH) 3 .
[0027] (2) Sm(MAA) 3 Synthesis
[0028] Put...
Embodiment 1
[0035] (1) Pre-polymerization: First, add samarium methacrylate to the mixture of octanoic acid and propylene glycol for mixing, and stir evenly to obtain a mixture of samarium methacrylate; then add samarium methacrylate mixture, azobisisobutyronitrile Add dibutyl phthalate into methyl methacrylate and stir evenly to form a polymerization solution, and react in a water bath at 70°C for 1 hour to obtain a prepolymer;
[0036] (2) Polymerization molding: first pour the prepolymer obtained in step 1 into the mold, then put the mold containing the prepolymer into a 45°C oven and keep it warm for 8 hours, then raise the oven temperature to 90°C Keep it warm for 2 hours, then let it cool down to room temperature naturally, and demould to get the finished product of plexiglass.
[0037] The amount of each component is shown in Table 1, and the test results of light transmittance and shielding property of the prepared plexiglass finished product are shown in Table 1.
Embodiment 2
[0039] (1) Pre-polymerization: First, add samarium methacrylate to the mixture of caprylic acid and propylene glycol for mixing, and stir evenly to obtain a mixture of samarium methacrylate; then add samarium methacrylate mixture, azobisisoheptanonitrile Add dioctyl sebacate into methyl methacrylate and stir evenly to form a polymerization solution, and react in a water bath at 80°C for 0.5 hours to obtain a prepolymer;
[0040] (2) Polymerization molding: first pour the prepolymer obtained in step 1 into the mold, then put the mold containing the prepolymer into a 60°C oven and keep it warm for 5 hours, then raise the oven temperature to 100°C Keep it warm for 4 hours, then let it cool down to room temperature naturally, and demould to get the finished product of organic glass.
[0041] The amount of each component is shown in Table 1, and the test results of light transmittance and shielding property of the prepared plexiglass finished product are shown in Table 1.
PUM
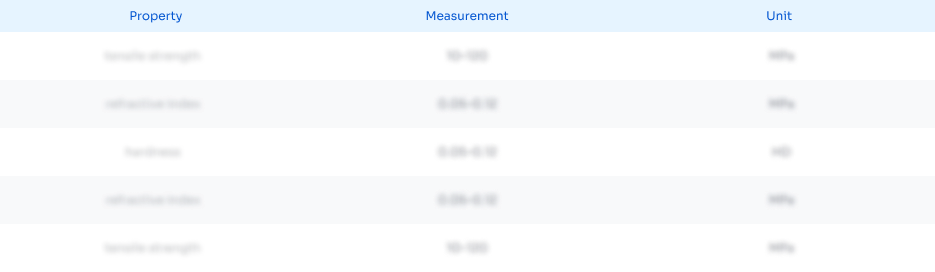
Abstract
Description
Claims
Application Information

- Generate Ideas
- Intellectual Property
- Life Sciences
- Materials
- Tech Scout
- Unparalleled Data Quality
- Higher Quality Content
- 60% Fewer Hallucinations
Browse by: Latest US Patents, China's latest patents, Technical Efficacy Thesaurus, Application Domain, Technology Topic, Popular Technical Reports.
© 2025 PatSnap. All rights reserved.Legal|Privacy policy|Modern Slavery Act Transparency Statement|Sitemap|About US| Contact US: help@patsnap.com