Method and device for machining airfoil hole on two-layer beam lining girder of automobile frame
A technology of automobile frame and processing method, which is applied in the directions of feeding device, positioning device, storage device, etc., can solve the problems of difficult production of multiple varieties, small batches, and multiple batches, large scale, and low processing efficiency.
- Summary
- Abstract
- Description
- Claims
- Application Information
AI Technical Summary
Problems solved by technology
Method used
Image
Examples
Embodiment Construction
[0018] The present invention will be further explained below in conjunction with the drawings and embodiments. In the following detailed description, only certain exemplary embodiments of the present invention are described by way of illustration. Needless to say, those of ordinary skill in the art can realize that the described embodiments can be modified in various ways without departing from the spirit and scope of the present invention. Therefore, the drawings and description are illustrative in nature, and are not used to limit the protection scope of the claims.
[0019] The method for processing double-layer beam lining beam wing hole of automobile frame includes the following steps:
[0020] Step 1. The plate of the main beam of the double-layer beam is fed into a flat-plate numerically controlled automatic punching and punching machine, and the web and wing holes of the double-layer beam main beam are completed by the flat-plate numerically controlled automatic punching a...
PUM
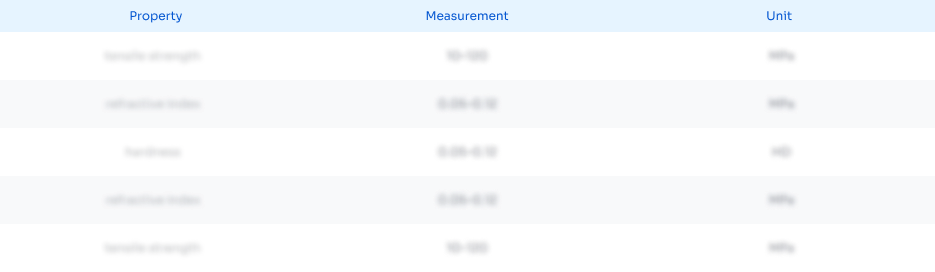
Abstract
Description
Claims
Application Information

- R&D
- Intellectual Property
- Life Sciences
- Materials
- Tech Scout
- Unparalleled Data Quality
- Higher Quality Content
- 60% Fewer Hallucinations
Browse by: Latest US Patents, China's latest patents, Technical Efficacy Thesaurus, Application Domain, Technology Topic, Popular Technical Reports.
© 2025 PatSnap. All rights reserved.Legal|Privacy policy|Modern Slavery Act Transparency Statement|Sitemap|About US| Contact US: help@patsnap.com