Roller rotary offset printing press having at least one coating unit with a chamber blade and an anilox roller
A web and printing machine technology, applied in the field of web pivoting lithographic printing machines, can solve the problems of high equipment consumption and achieve the effects of reducing costs, less space, and preventing ink or paint from blurring
- Summary
- Abstract
- Description
- Claims
- Application Information
AI Technical Summary
Problems solved by technology
Method used
Image
Examples
Embodiment 1
[0045] Example 1: "Directly, in a winding manner"
[0046] This example is also figure 1Visible in a). The printing substrate 06 is in direct contact with the anilox roller 02 during the printing process. The paint is transferred directly onto the printing material 06 from the depressions in the outer surface of the anilox roller 02 . The paint dots delivered by the individual depressions are more easily movable and connected to one another after their delivery, so that a continuous paint surface is achieved at the desired position on the printing material 06 . An anilox roll 02 with a relatively fine mesh is used for this, which means that in the case of linear structures the thread density is preferably between 90 and 130 threads per centimeter. The printing material 06 is wound and pressed onto the anilox roller 02, that is, the printing material 06 not only touches the anilox roller 02 on a straight line parallel to the rotation axis of the anilox roller 02, but also th...
Embodiment 2
[0048] Example 2: "Directly, by embossing"
[0049] This example is also figure 2 Visible in a). The printing material 06 is coated directly by the anilox roller 02 as in Example 1. The anilox roller 02 is designed as in Example 1 and the transfer of the coating is also carried out exactly as in Example 1, where the transferred coating spots also move to desired positions on the printing material 06 to form a through coating surface. The embossing roller 08 presses the printing material 06 against the anilox roller 02 in order to achieve a better contact between the anilox roller 02 and the printing material 06 and thus improve the exit of the paint from the recessed part of the anilox roller 02 to the printing material Pass on 06. The printing material 06 can be wound around the anilox roller 02 and / or the embossing roller 08 or can also be guided in a straight line between the anilox roller 02 and the embossing roller 08 , ie the contact area between the printing materia...
Embodiment 3
[0051] Example 3: "With applicator roll, in a winding manner"
[0052] This example is also image 3 Visible in a). The anilox roller 02 is in contact with the applicator roller 07 in addition to the chambered doctor blade 03 . The applicator roller 07 is again in rolling contact with the printing material 06 . Since the printing material 06 is not in direct contact with the anilox roller 02 , the linear density of the recesses in the outer surface of the anilox roller 02 preferably lies in the range of 40 to 80 threads per centimeter. The printing material 06 wraps around the applicator roller 07, so that the contact between the applicator roller 07 and the printing material 06 is not designed as a line but as a plane, and a compression between the printing material 06 and the applicator roller 07 takes place force. From within the chambered doctor blade 3 , the paint is transferred via the anilox roller 02 to the applicator roller 07 and from there onto the printing mate...
PUM
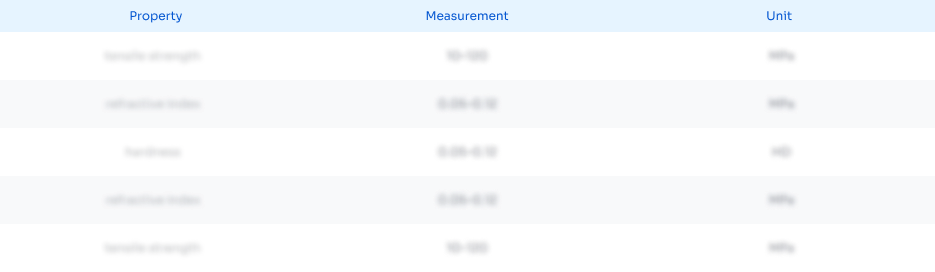
Abstract
Description
Claims
Application Information

- R&D
- Intellectual Property
- Life Sciences
- Materials
- Tech Scout
- Unparalleled Data Quality
- Higher Quality Content
- 60% Fewer Hallucinations
Browse by: Latest US Patents, China's latest patents, Technical Efficacy Thesaurus, Application Domain, Technology Topic, Popular Technical Reports.
© 2025 PatSnap. All rights reserved.Legal|Privacy policy|Modern Slavery Act Transparency Statement|Sitemap|About US| Contact US: help@patsnap.com