Flexible loading system of friction and wear testing machine
A flexible loading system, friction and wear test technology, applied in the direction of testing wear resistance, strength characteristics, measuring devices, etc., can solve the system can not be loaded steplessly, load pop and other problems, to solve the impact problem, expand the test range, The effect of reducing labor intensity
- Summary
- Abstract
- Description
- Claims
- Application Information
AI Technical Summary
Problems solved by technology
Method used
Image
Examples
Embodiment Construction
[0018] As shown in the figure, a flexible loading system of a friction and wear testing machine includes a frame 1, a loading cylinder 2, a servo valve 3, a displacement sensor 4, a load sensor 5, a torque sensor 6, a friction disc 7, a friction pin 8, Guide device 9, hydraulic system and servo controller; loading oil cylinder 2 is horizontally arranged on the frame 1, the piston rod 10 of loading oil cylinder 2 is a hollow structure, the piston rod 10 runs through the cylinder body of loading oil cylinder 2, and one end of the piston rod 10 is arranged There is a displacement sensor 4, the other end of which is connected to the load sensor 5. The displacement sensor 4 is a differential transformer type displacement sensor. The shell of the displacement sensor 4 is fixed on the frame 1. The measuring iron core 11 of the displacement sensor 4 passes through the piston rod 10 and the The load sensor 5 is connected; the friction pin 8 is set on the load sensor 5, the friction dis...
PUM
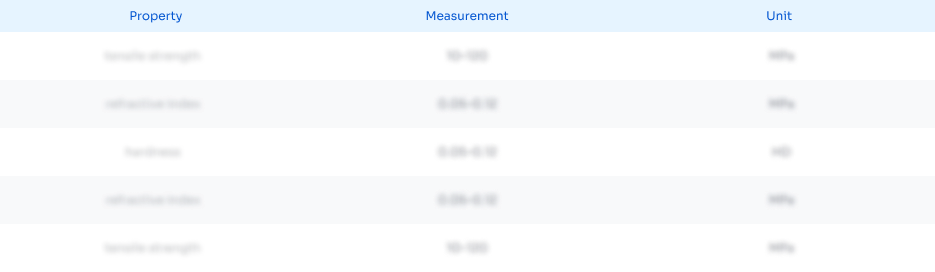
Abstract
Description
Claims
Application Information

- R&D Engineer
- R&D Manager
- IP Professional
- Industry Leading Data Capabilities
- Powerful AI technology
- Patent DNA Extraction
Browse by: Latest US Patents, China's latest patents, Technical Efficacy Thesaurus, Application Domain, Technology Topic, Popular Technical Reports.
© 2024 PatSnap. All rights reserved.Legal|Privacy policy|Modern Slavery Act Transparency Statement|Sitemap|About US| Contact US: help@patsnap.com