Furnace with multiple heat recovery systems
A melting furnace and heat-generating technology, applied in the field of glass manufacturing, can solve the problems of unsuitable air-burning regenerative or reheating furnaces
- Summary
- Abstract
- Description
- Claims
- Application Information
AI Technical Summary
Problems solved by technology
Method used
Image
Examples
example
[0056] Table 1 shows an illustrative comparison of energy balances for: (Case 1) 450 short tpd regenerative vessel glass melting furnace with five ports to regenerative indirect heat exchangers; (Case 2) Same furnace with conventional raw cullet preheater preheating raw / cullet to 572°F; (Case 3) Modified 450 short tpd regenerative vessel glass melting furnace with There is a first pair of ports that converts to continuous vent line ports according to the invention to preheat raw / cullet to 932°F; (Case 4) Modified 450 short tpd regenerative vessel glass melting furnace , with a first pair of ports converted to continuous snorkel ports and a second pair of ports closed and replaced by one or two pairs of oxy-fuel burners according to the invention , to preheat raw / cullet to 932°F. Table 2 shows the corresponding conditions and assumptions for the performance of these regenerators.
[0057] In all cases a 50:50 mix of raw material to cullet was assumed. Case 1 represents the b...
PUM
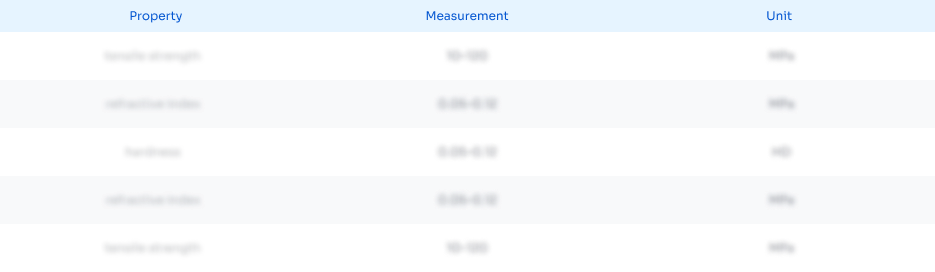
Abstract
Description
Claims
Application Information

- R&D
- Intellectual Property
- Life Sciences
- Materials
- Tech Scout
- Unparalleled Data Quality
- Higher Quality Content
- 60% Fewer Hallucinations
Browse by: Latest US Patents, China's latest patents, Technical Efficacy Thesaurus, Application Domain, Technology Topic, Popular Technical Reports.
© 2025 PatSnap. All rights reserved.Legal|Privacy policy|Modern Slavery Act Transparency Statement|Sitemap|About US| Contact US: help@patsnap.com