Production method for electrolytic manganese dioxide
An electrolytic manganese dioxide, production method technology, applied in chemical instruments and methods, cleaning methods using liquids, electrolytic components, etc., can solve the problem that the pH value of electrolytic manganese dioxide products cannot be well controlled, and the High-quality electrolytic manganese dioxide products cannot be removed well, etc., to achieve good economic and social benefits, low production costs, and improved quality.
- Summary
- Abstract
- Description
- Claims
- Application Information
AI Technical Summary
Problems solved by technology
Method used
Image
Examples
Embodiment 1
[0031] A production method for special electrolytic manganese dioxide for high-performance mercury-free alkaline batteries, comprising the following steps:
[0032] A. Preparation of the mixed solution of crude manganese sulfate and pulp: low-grade manganese oxide ore powder with -200 mesh particle size reaching 90%-95% (low-grade manganese oxide ore powder contains 17.16% manganese quality), -120 mesh particle size reaching 90% -95% high-activity pyrite powder (high-activity pyrite powder contains 35% sulfur content), 98% industrial sulfuric acid, and electrolytic waste liquid are put into the leaching reaction tank with constant stirring according to a certain material ratio, and leaching is carried out. The effective volume of the reaction tank is 70m 3 , the reaction temperature in the process is controlled at 95 ° C, and the time is started from the end of feeding to 95 ° C after heating, and the reaction time is 3.5 hours, that is, generally when the pH value reaches 3.0...
Embodiment 2
[0043] A production method for special electrolytic manganese dioxide for high-performance mercury-free alkaline batteries, comprising the following steps:
[0044] A. Preparation of the mixed solution of crude manganese sulfate and pulp: the low-grade manganese oxide ore powder with a particle size of -200 mesh reaching 90%-95% (the mass of low-grade manganese oxide ore powder contains 18%), and the particle size of -120 mesh reaching 90% -95% of high-activity pyrite powder (high-activity pyrite powder has a sulfur content of 40%), 98% of industrial sulfuric acid, and electrolytic waste liquid are put into the leaching reaction tank with constant stirring according to a certain material ratio. The reaction temperature was controlled at 92°C, and the timing was started from the end of feeding the material until the heating reached 92°C. The reaction time was 4 hours, that is, when the pH value reached 3.0 to 3.8, it indicated that the leaching reaction had been completed, and a...
Embodiment 3
[0055] A production method for special electrolytic manganese dioxide for high-performance mercury-free alkaline batteries, comprising the following steps:
[0056] A. Preparation of the mixed solution of crude manganese sulfate and pulp: low-grade manganese oxide ore powder with -200 mesh particle size reaching 90%-95% (low-grade manganese oxide ore powder contains 16% manganese quality), -120 mesh particle size reaching 90% -95% of high-activity pyrite powder (high-activity pyrite powder has a sulfur content of 38%), 98% of industrial sulfuric acid and electrolytic waste liquid are put into the leaching reaction tank with constant stirring according to a certain material ratio. The reaction temperature was controlled at 94°C, and the timing was started from the end of feeding the material until the heating reached 94°C, and the reaction time was 4 hours, that is, when the pH value reached 3.0 to 3.8, it indicated that the leaching reaction had been completed, and a mixed solu...
PUM
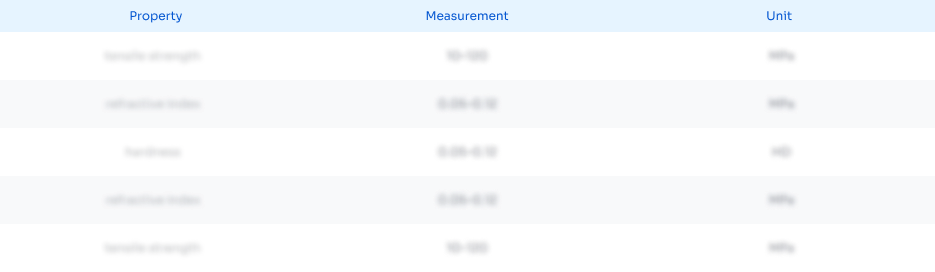
Abstract
Description
Claims
Application Information

- R&D
- Intellectual Property
- Life Sciences
- Materials
- Tech Scout
- Unparalleled Data Quality
- Higher Quality Content
- 60% Fewer Hallucinations
Browse by: Latest US Patents, China's latest patents, Technical Efficacy Thesaurus, Application Domain, Technology Topic, Popular Technical Reports.
© 2025 PatSnap. All rights reserved.Legal|Privacy policy|Modern Slavery Act Transparency Statement|Sitemap|About US| Contact US: help@patsnap.com