CBN cutting tool bit for sintered steels
A technology for cutting blades and steel materials, which is applied to metal sawing equipment, knives of sawing machine devices, metal processing equipment, etc., can solve the problems of high power consumption, thick disc-shaped steel plates, and easy pollution of the environment, and achieve reasonable structure, Smooth cutting and fast chip removal
- Summary
- Abstract
- Description
- Claims
- Application Information
AI Technical Summary
Problems solved by technology
Method used
Image
Examples
Embodiment Construction
[0014] From figure 1 , figure 2 , image 3 It can be seen that: a CBN sintered steel cutting head is characterized by:
[0015] The CBN sintered steel cutting head is mainly composed of an integrated non-working layer 1 (non-cutting body) and a working layer 2 (cutting body). The lower end of the CBN sintered steel cutting head is a rectangular parallelepiped non-working layer 1 , the non-working layer 1 is composed of metal bond (binder) powder, and the upper part (on the upper surface) of the non-working layer 1 is vertically provided with a corrugated working layer 2 from left to right, and the corrugated working layer Each adjacent hypotenuse of layer 2 intersects at an included angle of 30°-120°, and each intersecting part is dislocated evenly before and after on the non-working layer 1. Each adjacent hypotenuse of the corrugated working layer 2 (cutting body) In particular, it is best to intersect at an angle of 60°-90°. The gaps between the hypotenuses intersecting ...
PUM
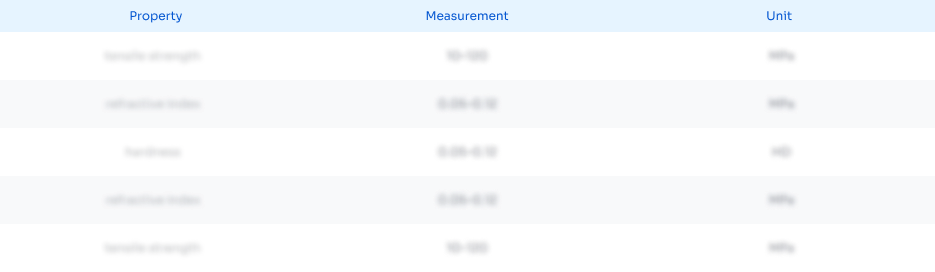
Abstract
Description
Claims
Application Information

- Generate Ideas
- Intellectual Property
- Life Sciences
- Materials
- Tech Scout
- Unparalleled Data Quality
- Higher Quality Content
- 60% Fewer Hallucinations
Browse by: Latest US Patents, China's latest patents, Technical Efficacy Thesaurus, Application Domain, Technology Topic, Popular Technical Reports.
© 2025 PatSnap. All rights reserved.Legal|Privacy policy|Modern Slavery Act Transparency Statement|Sitemap|About US| Contact US: help@patsnap.com