Calibration and loading method of air-floating multidimensional force transducer
A multi-dimensional force sensor and load cell technology, applied in the direction of force/torque/power measuring instrument calibration/testing, instruments, measuring devices, etc., can solve the problems of complex loading device and complicated adjustment, and achieve simple loading device and easy operation Convenience, high loading accuracy effect
- Summary
- Abstract
- Description
- Claims
- Application Information
AI Technical Summary
Problems solved by technology
Method used
Image
Examples
Embodiment Construction
[0020] This embodiment is aimed at the air-floating multi-dimensional force sensor disclosed in the invention patent of ZL200810019550.2. The center of gravity of the floating plate 1 in the air-floating multi-dimensional force sensor is set to coincide with its geometric center, and the gravity of the floating plate 1 is mg; Set up two space Cartesian coordinate systems with the center of gravity of the floating plate 1 as the origin, one is a fixed coordinate system x-y-z in which the z-axis direction is parallel to the direction of gravity; the other is a fixed coordinate system in which the z-axis direction is parallel to the thickness direction of the floating plate 1 Floating plate position coordinate system X-Y-Z; at the initial position, the fixed coordinate system x-y-z coincides with the position of the floating plate position coordinate system X-Y-Z. The angles are all 0; when calibrating and loading, the entire air-floating six-dimensional force sensor is tilted at ...
PUM
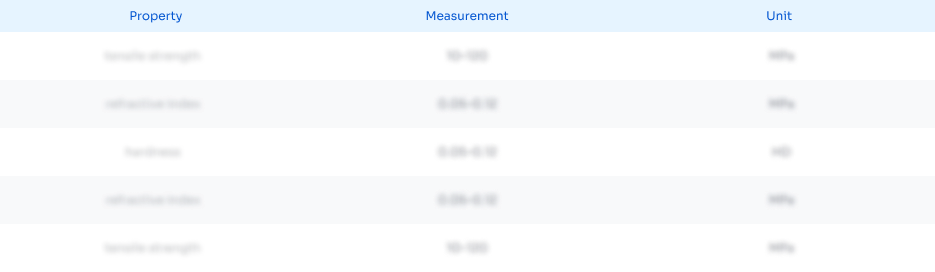
Abstract
Description
Claims
Application Information

- Generate Ideas
- Intellectual Property
- Life Sciences
- Materials
- Tech Scout
- Unparalleled Data Quality
- Higher Quality Content
- 60% Fewer Hallucinations
Browse by: Latest US Patents, China's latest patents, Technical Efficacy Thesaurus, Application Domain, Technology Topic, Popular Technical Reports.
© 2025 PatSnap. All rights reserved.Legal|Privacy policy|Modern Slavery Act Transparency Statement|Sitemap|About US| Contact US: help@patsnap.com