Process for treating and recycling di-tertiary-butyl peroxide production waste water
A technology of di-tert-butyl peroxide and waste water production, which is applied in the directions of alkali metal oxide/hydroxide, water/sewage multi-stage treatment, water/sludge/sewage treatment, etc.
- Summary
- Abstract
- Description
- Claims
- Application Information
AI Technical Summary
Problems solved by technology
Method used
Examples
Embodiment 1
[0025] (1) Treatment of strong acid wastewater
[0026] Collect 12 liters of waste acid produced by tert-butyl peroxide from the blowdown outlet of the production unit. Which contains sulfuric acid> 40%, COD cr =83460.96mg / L.
[0027] Add 12 grams of sodium sulfite to the waste acid (1 gram of sodium sulfite per liter of waste water), slowly heat to 70°C, stir for 1.5 hours and then distill under normal pressure. phase, and the lower layer is the aqueous phase. The organic phase of the upper layer was recovered, and 1000ml of a mixture of tert-butanol and tert-butyl peroxide was obtained after distillation and dehydration by heterogeneous phase separation technology. The total content was 92.21% through gas chromatography analysis, which could be reused in production. The aqueous phase was refluxed. When the distillate has no stratification at room temperature, continue to distill to separate low-concentration acidic wastewater. The collected low-concentration acidic wast...
Embodiment 2
[0034] (1) Treatment of strong acid wastewater
[0035] With embodiment 1.
[0036] (2) Treatment of di-tert-butyl peroxide alkaline washing wastewater
[0037] Get 23 liters of di-tert-butyl peroxide alkali washing wastewater from the blowdown outlet of the production unit. of which COD cr =5288.16mg / L, containing 13.92% non-volatile solids, pale yellow and turbid.
[0038] Heat di-tert-butyl peroxide alkaline washing wastewater to 70°C, add 23 grams of sodium sulfide (1 gram of sodium sulfide per liter of waste liquid) and stir to generate gas and flocculent precipitates, and filter out flocculent precipitates. The filtrate is distilled under reduced pressure by the water circulation pump to produce low-concentration alkaline wastewater, the pH value of low-concentration alkaline wastewater is 9-10, COD cr =1635.00mg / L, CODcr removal rate 69.01%. After the low-concentration wastewater is neutralized to pH = 7-8, it is discharged after hydrolysis-contact oxidation and 3...
PUM
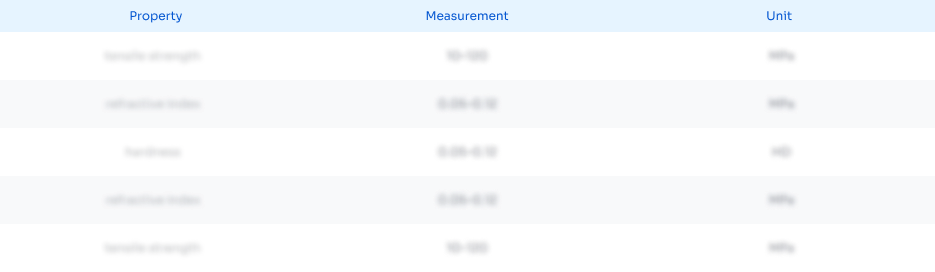
Abstract
Description
Claims
Application Information

- R&D
- Intellectual Property
- Life Sciences
- Materials
- Tech Scout
- Unparalleled Data Quality
- Higher Quality Content
- 60% Fewer Hallucinations
Browse by: Latest US Patents, China's latest patents, Technical Efficacy Thesaurus, Application Domain, Technology Topic, Popular Technical Reports.
© 2025 PatSnap. All rights reserved.Legal|Privacy policy|Modern Slavery Act Transparency Statement|Sitemap|About US| Contact US: help@patsnap.com