Design method of permanent magnet motor capable of reducing cogging effect and permanent magnet motor
A technology of permanent magnet motor and cogging effect, which is applied in the direction of magnetic circuit shape/style/structure, salient pole, etc., can solve the problem of permanent magnet motor torque constant/thrust constant decrease, and achieve reduction of cogging torque/ Effects of cogging force, peak reduction, and harmonic component reduction
- Summary
- Abstract
- Description
- Claims
- Application Information
AI Technical Summary
Problems solved by technology
Method used
Image
Examples
Embodiment Construction
[0061] see Figure 3-6, the present invention selects an appropriate curved surface permanent magnet, or a permanent magnet that is properly chamfered, and divides the single permanent magnet of each magnetic pole into several permanent magnet small pieces along the circumferential direction of the rotary motor or the moving direction of the linear motor. The permanent magnets are arranged on the surface of the stator or the mover at a certain distance, which can reduce the peak value of single-tooth cogging torque / cogging force, reduce complex harmonic components, and effectively reduce the cogging torque / cogging force of surface permanent magnet motors. cogging forces and reduce costs.
[0062] Using the analytical or numerical calculation method of the electromagnetic field, with the goal of minimizing the cogging torque / cogging force of the permanent magnet motor, the single permanent magnet of each magnetic pole is optimally divided into two parts along the circumferentia...
PUM
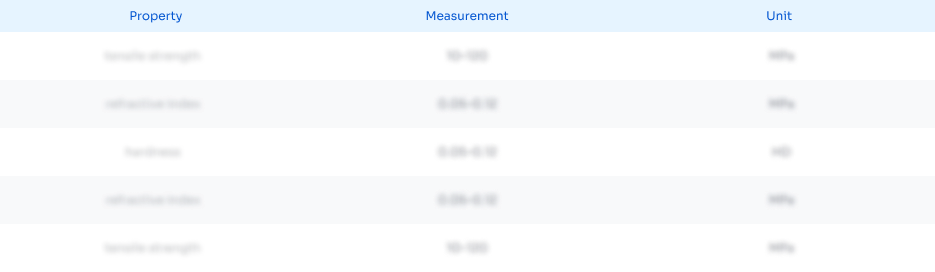
Abstract
Description
Claims
Application Information

- R&D Engineer
- R&D Manager
- IP Professional
- Industry Leading Data Capabilities
- Powerful AI technology
- Patent DNA Extraction
Browse by: Latest US Patents, China's latest patents, Technical Efficacy Thesaurus, Application Domain, Technology Topic, Popular Technical Reports.
© 2024 PatSnap. All rights reserved.Legal|Privacy policy|Modern Slavery Act Transparency Statement|Sitemap|About US| Contact US: help@patsnap.com