Board thickness controller for rolling machine
A control device and plate thickness technology, which is applied in the rolling mill control device, rolling force/roll gap control, metal rolling, etc., can solve the problems of rotation angle change, etc., and achieve the effect of suppressing plate thickness fluctuation
- Summary
- Abstract
- Description
- Claims
- Application Information
AI Technical Summary
Problems solved by technology
Method used
Image
Examples
Embodiment approach 1
[0047] figure 1 It is a configuration diagram showing a thickness control device for a rolling mill according to Embodiment 1 of the present invention, figure 2 is for illustration figure 1 A diagram of the specific functions of the plate thickness control device of the rolling mill shown. exist figure 1 In the figure, reference numeral 1 is a rolled material such as a steel plate rolled by a rolling mill, which is rolled by work rolls 2 and 3 arranged up and down. Reference numerals 4 and 5 denote backup rolls that support the work rolls 2 and 3 from above and below.
PUM
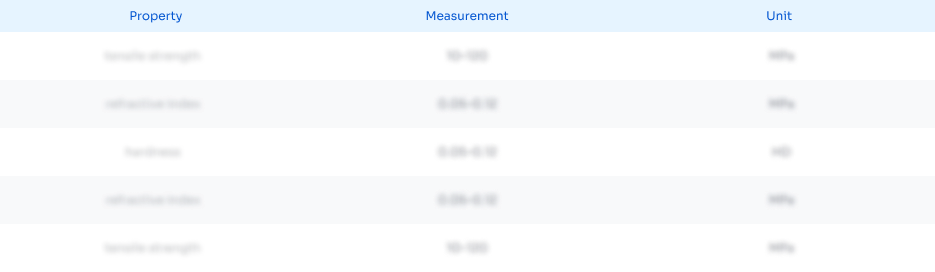
Abstract
Description
Claims
Application Information

- R&D
- Intellectual Property
- Life Sciences
- Materials
- Tech Scout
- Unparalleled Data Quality
- Higher Quality Content
- 60% Fewer Hallucinations
Browse by: Latest US Patents, China's latest patents, Technical Efficacy Thesaurus, Application Domain, Technology Topic, Popular Technical Reports.
© 2025 PatSnap. All rights reserved.Legal|Privacy policy|Modern Slavery Act Transparency Statement|Sitemap|About US| Contact US: help@patsnap.com