Double-permanent magnet outer-rotor permanent magnet biased radial magnetic bearing
A technology of permanent magnetic bias and double permanent magnets, which is applied in the direction of bearings, shafts and bearings, shafts, etc., can solve the problems of magnetic interference of other components, increase the volume of the device, and complicate compensation methods, so as to reduce the residual magnetic moment and overcome the problems Sophisticated, easy to install and reliable results
- Summary
- Abstract
- Description
- Claims
- Application Information
AI Technical Summary
Benefits of technology
Problems solved by technology
Method used
Image
Examples
Embodiment Construction
[0018] Such as figure 1 , 2 As shown, a dual permanent magnet external rotor permanent magnet bias radial magnetic bearing consists of an outer magnetic ring 1, an outer permanent magnet 8, a stator core 3, an excitation coil 4, an inner magnetic ring 5, an inner permanent magnet 2 and The rotor core is composed of 6, each stator core 3 is composed of 4 magnetic poles, and 2 stator cores 3 are composed of 8 magnetic poles at the left and right ends of the magnetic bearing, which respectively form the magnetic poles in the positive and negative directions of the X and Y axes. Each stator magnetic pole is wound with an excitation The coil 4, the rotor core 6 outside the stator core 3, the outer magnetic ring 1 outside the rotor core 6, the outer permanent magnet 8 is located between the two outer magnetic rings 1, the inner surface of the rotor core 6 and the outer surface of the stator core 3 remain There is a certain gap, forming an air gap 7 , the radial inner part of the st...
PUM
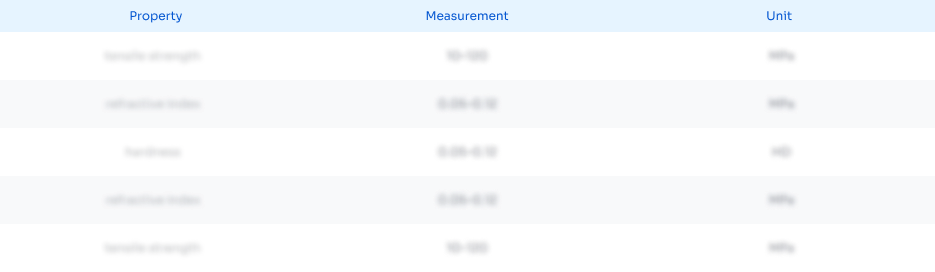
Abstract
Description
Claims
Application Information

- R&D
- Intellectual Property
- Life Sciences
- Materials
- Tech Scout
- Unparalleled Data Quality
- Higher Quality Content
- 60% Fewer Hallucinations
Browse by: Latest US Patents, China's latest patents, Technical Efficacy Thesaurus, Application Domain, Technology Topic, Popular Technical Reports.
© 2025 PatSnap. All rights reserved.Legal|Privacy policy|Modern Slavery Act Transparency Statement|Sitemap|About US| Contact US: help@patsnap.com