Bearing seat with oil return groove
A technology of bearing seat and oil groove, applied in the direction of bearing components, shafts and bearings, rigid supports of bearing components, etc., can solve the problems of difficult and troublesome oil drainage, and achieve the effect of clean oil replacement
- Summary
- Abstract
- Description
- Claims
- Application Information
AI Technical Summary
Problems solved by technology
Method used
Image
Examples
Embodiment Construction
[0015] A bearing seat with an oil return groove, comprising a seat cover 8, a seat bottom 12, a shaft hole, a bearing rack 7, an oil filling hole 6, an oil discharge hole 15, a labyrinth groove 2, an engaging screw hole 10, and an oil chamber 16, and is characterized in that : the bottom side of the labyrinth groove 2 at the bottom of the seat 12 is provided with an oil return groove 14 to communicate with the oil chamber 16, and the oil discharge hole 15 is located directly below the center of the bottom oil chamber 16 of the seat bottom 12.
[0016] A bearing temperature detection hole 4 communicating with the bearing rack 7 is provided on the side of the base 12 .
[0017] An oil temperature detection hole 3 communicating with the oil chamber 16 is provided on the side of the base 12 .
[0018] The bottom surface 17 of the oil chamber is set at a certain slope 18 .
[0019] The slope 18 of the bottom surface 17 of the oil chamber is preferably 3-5°.
[0020] Seat cover 8 ...
PUM
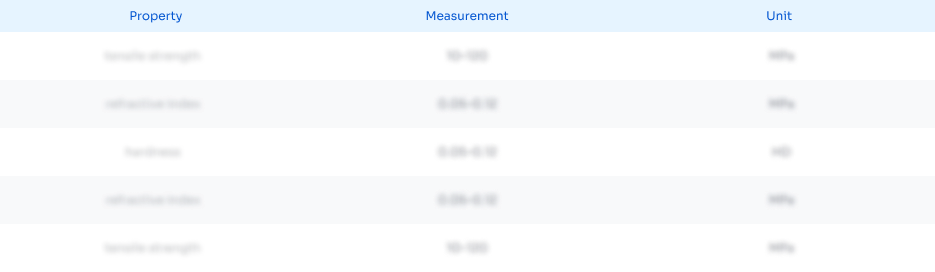
Abstract
Description
Claims
Application Information

- R&D Engineer
- R&D Manager
- IP Professional
- Industry Leading Data Capabilities
- Powerful AI technology
- Patent DNA Extraction
Browse by: Latest US Patents, China's latest patents, Technical Efficacy Thesaurus, Application Domain, Technology Topic, Popular Technical Reports.
© 2024 PatSnap. All rights reserved.Legal|Privacy policy|Modern Slavery Act Transparency Statement|Sitemap|About US| Contact US: help@patsnap.com