Technology for reducing allowance cutting during ship building
A margin and ship technology, applied in ship construction, ship parts, ships, etc., can solve the problems of unbalanced gap, easy deformation, inadequate welding and other problems, reduce the workload of the slipway, avoid the amount of secondary cutting, reduce The effect of shipbuilding costs
- Summary
- Abstract
- Description
- Claims
- Application Information
AI Technical Summary
Problems solved by technology
Method used
Image
Examples
Embodiment Construction
[0030] In the hull construction process of a 1000-ton scientific research ship, the technical scheme of the present invention is adopted, and the specific implementation method is:
[0031] 1. Parts lofting and blanking steps
[0032] According to the "Hull Segmentation Map and Surplus Distribution Map", the hull is divided into 7 general sections, from the stern to the bow, they are Ⅰ general section, Ⅱ general section, Ⅲ general section, Ⅳ general section, Ⅴ general section, and Ⅵ general section. Segment, general section VII, respectively inserting or butt-jointing the segments, etc., and adding additional segmental surplus to the deck, outer plate, longitudinal, rib, strong rib, wall plate and other structures of each typical node. The information on the quantity, berth margin, and compensation amount is implemented in the information of computer blanking. The material is cut in place at one time, and it can be assembled and welded directly on site. It is not necessary ...
PUM
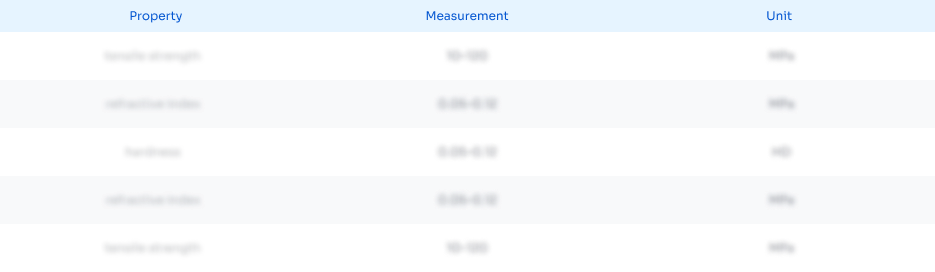
Abstract
Description
Claims
Application Information

- Generate Ideas
- Intellectual Property
- Life Sciences
- Materials
- Tech Scout
- Unparalleled Data Quality
- Higher Quality Content
- 60% Fewer Hallucinations
Browse by: Latest US Patents, China's latest patents, Technical Efficacy Thesaurus, Application Domain, Technology Topic, Popular Technical Reports.
© 2025 PatSnap. All rights reserved.Legal|Privacy policy|Modern Slavery Act Transparency Statement|Sitemap|About US| Contact US: help@patsnap.com