Automatic control method for camber and wedge of hot rolled strip roughing mill
A technology of hot-rolled strip steel and rough-rolling units, applied in the direction of rolling mill control devices, metal rolling, metal rolling, etc., which can solve the problems of inability to analyze and find the cause, inability to analyze the essential cause of camber, and high requirements for installation and debugging
- Summary
- Abstract
- Description
- Claims
- Application Information
AI Technical Summary
Problems solved by technology
Method used
Image
Examples
Embodiment Construction
[0060] The technical solution of the present invention will be further described below in conjunction with the accompanying drawings and a preferred embodiment.
[0061] The camber or wedge-shaped automatic control process of this embodiment is applied to the hot-rolled strip rough-rolling unit, which forms a camber-shaped or wedge-shaped automatic control by adding an auxiliary control module in the hot-rolled strip rough-rolling mill control system. system (such as figure 1 As shown, referred to as ACC), the process includes: ACC input data processing, ACC control cycle setting, ACC controller calculation and ACC control quantity output (refer to figure 2 ).
[0062] The implementation process of the camber or wedge automatic control process will be described in detail as follows.
[0063] 1. ACC control mode definition and start and stop time
[0064] There are two control modes of ACC, one is the billet to billet (bar to bar) mode, which is used in the secondary system...
PUM
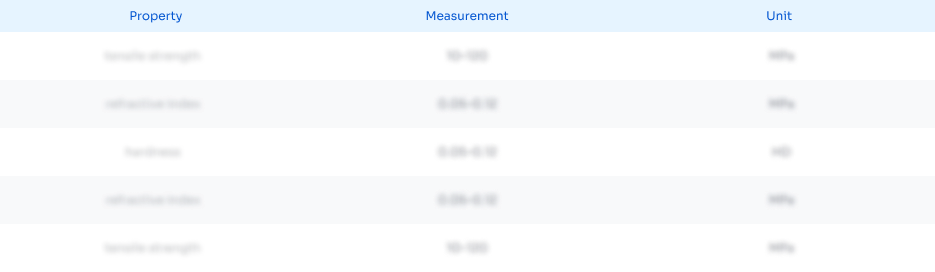
Abstract
Description
Claims
Application Information

- R&D Engineer
- R&D Manager
- IP Professional
- Industry Leading Data Capabilities
- Powerful AI technology
- Patent DNA Extraction
Browse by: Latest US Patents, China's latest patents, Technical Efficacy Thesaurus, Application Domain, Technology Topic, Popular Technical Reports.
© 2024 PatSnap. All rights reserved.Legal|Privacy policy|Modern Slavery Act Transparency Statement|Sitemap|About US| Contact US: help@patsnap.com