Acrylic modified epoxy resin emulsion and preparation method thereof
An epoxy resin emulsion, epoxy resin technology, applied in the direction of coating, can solve problems such as ecological environment damage, and achieve the effects of low cost, good water resistance, and good emulsion stability
- Summary
- Abstract
- Description
- Claims
- Application Information
AI Technical Summary
Problems solved by technology
Method used
Image
Examples
Embodiment 1
[0031] Embodiment 1: Preparation of reactive anionic nonionic epoxy resin emulsifier
[0032] (1) Take 0.1mol epoxy resin E-51, 0.1mol fatty alcohol polyoxyethylene ether C 12 h 25 (CH 2 CH 2 O) 7 H and 0.44 g of triphenylphosphine were placed in a four-necked flask, reacted at 90° C. for 1 h, and then heated to 100° C. to continue the reaction for 3 h to obtain polyoxyethylene ether monoester of epoxy resin.
[0033] (2) Cool down the epoxy resin polyoxyethylene ether monoester obtained in (1) to 70°C, weigh 0.1 mol of taurine and slowly add it dropwise into a four-necked flask, and continue the reaction for 3 hours after the addition is completed, and then finish the reaction by adding 27g of NaOH aqueous solution with a mass concentration of 15% was neutralized and dispersed to obtain a reactive anion-nonionic epoxy resin emulsifier.
Embodiment 2
[0034] Embodiment 2: Preparation of reactive anionic nonionic epoxy resin emulsifier
[0035] (1) Take 0.1mol epoxy resin E-44, 0.1mol fatty alcohol polyoxyethylene ether C 12 h 25 (CH 2 CH 2 O) 9 H and 1.02 g of triphenylphosphine were placed in a four-necked flask, reacted at 90°C for 1 hour, and then heated to 110°C to continue the reaction for 3 hours to obtain polyoxyethylene ether monoester of epoxy resin.
[0036] (2) Cool down the epoxy resin polyoxyethylene ether monoester obtained in (1) to 70°C, weigh 0.1 mol of N-methyl taurine and slowly drop it into a four-necked flask, and continue the reaction for 3 hours after the addition is completed. After finishing the reaction, 20g of NaOH solution with a mass concentration of 20% was neutralized and dispersed to obtain a reactive anion-nonionic epoxy resin emulsifier.
Embodiment 3
[0037] Embodiment 3: the preparation of reactive anionic nonionic epoxy resin emulsifier
[0038] (1) Take 0.1mol epoxy resin E-44, 0.1mol fatty alcohol polyoxyethylene ether C 12 h 25 (CH 2 CH 2 O) 15 H and 1.28 g of triphenylphosphine were placed in a four-necked flask, and reacted at 110° C. for 4 hours to obtain polyoxyethylene ether monoester of epoxy resin.
[0039] (2) Cool down the epoxy resin polyoxyethylene ether monoester obtained in (1) to 90° C., weigh 0.1 mol of N-methyl taurine and slowly drop it into a four-necked flask, and continue the reaction for 2 hours after the addition is completed. After finishing the reaction, 20g of NaOH solution with a mass concentration of 20% was neutralized and dispersed to obtain a reactive anion-nonionic epoxy resin emulsifier.
PUM
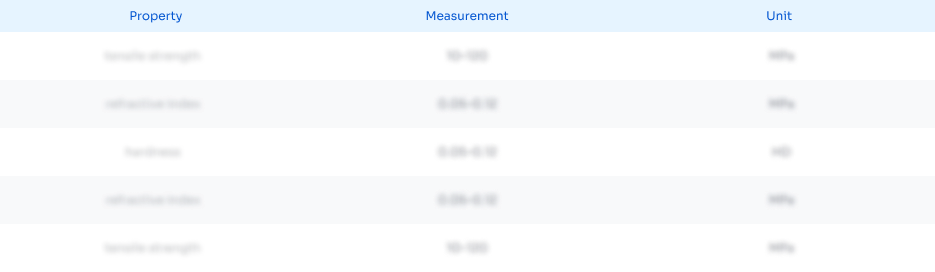
Abstract
Description
Claims
Application Information

- R&D
- Intellectual Property
- Life Sciences
- Materials
- Tech Scout
- Unparalleled Data Quality
- Higher Quality Content
- 60% Fewer Hallucinations
Browse by: Latest US Patents, China's latest patents, Technical Efficacy Thesaurus, Application Domain, Technology Topic, Popular Technical Reports.
© 2025 PatSnap. All rights reserved.Legal|Privacy policy|Modern Slavery Act Transparency Statement|Sitemap|About US| Contact US: help@patsnap.com