Double-face riveting press of HDMI (High-Definition Multimedia Interface) terminal
An HDMI terminal, riveting press technology, applied in electrical components, circuits, connections, etc., can solve the problems of not meeting energy saving and consumption reduction, increasing product costs, wasting working time, etc., to achieve compact structure, saving equipment costs, and easy operation. Effect
- Summary
- Abstract
- Description
- Claims
- Application Information
AI Technical Summary
Problems solved by technology
Method used
Image
Examples
Embodiment 1
[0025] figure 2 and image 3 This is a schematic diagram of the structure of the HDMI terminal double-sided riveting machine in the first embodiment. Its specific structure is mainly composed of a frame 21, a transmission device 22, a sliding assembly 23, and a fixing assembly 24. The frame 21 includes an upper beam 21.1 , the left and right uprights 21.2 and the base 21.3, the upper ends of the left and right uprights 21.2 are fixedly connected with the upper beam 21.1, the lower ends are fixed on the base 21.3, the transmission device 22 is installed on the frame 21, Equipped with a 280W power motor as a power source, a mechanical transmission device 22 is used. The mechanical transmission device 22 includes a transmission wheel 22.2 and a transmission shaft 22.1. The transmission shaft 22.1 is a crankshaft. For connection, a clutch device is arranged between the transmission wheel 22.2 and the crankshaft, and a clutch lever 22.3 is arranged on the clutch device. The crank...
Embodiment 2
[0028] Figure 4 and Figure 5 The schematic diagram of the structure of the HDMI terminal double-sided riveting machine in the second embodiment, the basic structure is basically the same as that in the first embodiment, and there are three main differences. First, the power source is an oil pump, and the transmission device 22 is an oil cylinder 22.4. The transmission shaft 22.1 is the telescopic rod of the oil cylinder 22.4, which is connected with the sliding block 23.1 of the sliding assembly 23 through the telescopic rod of the oil cylinder 22.4; 23 is connected with the sliding positioning rod 26 in a sliding fit; the third is that there is no clutch device.
Embodiment 3
[0030] The same as the second embodiment, the difference is that the power source used is a pressure pump, and the transmission device 22 thereof is a cylinder.
PUM
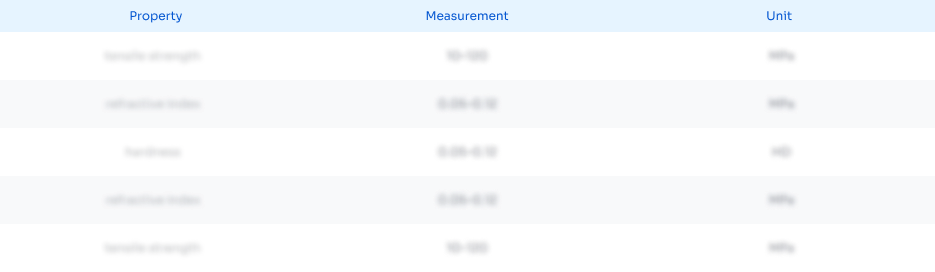
Abstract
Description
Claims
Application Information

- R&D Engineer
- R&D Manager
- IP Professional
- Industry Leading Data Capabilities
- Powerful AI technology
- Patent DNA Extraction
Browse by: Latest US Patents, China's latest patents, Technical Efficacy Thesaurus, Application Domain, Technology Topic, Popular Technical Reports.
© 2024 PatSnap. All rights reserved.Legal|Privacy policy|Modern Slavery Act Transparency Statement|Sitemap|About US| Contact US: help@patsnap.com