Thickness control method of finish roller strip steel and device
A technology of thickness control and strip steel, which is applied in the direction of rolling force/roll gap control, etc., can solve problems such as connection, increase cost, and inability to overcome model errors, and achieve the effect of improving control accuracy
- Summary
- Abstract
- Description
- Claims
- Application Information
AI Technical Summary
Problems solved by technology
Method used
Image
Examples
Embodiment 1
[0033] Such as figure 1 The schematic flow chart of Embodiment 1 of the thickness control method of a kind of finished strip steel shown in the present invention includes:
[0034] S11, acquiring simultaneous point measured data and same point measured data;
[0035] The obtained data include the original simultaneous point measured data and the original same point measured data of the parameters related to the rolling force and roll gap, such as rolling force, roll speed, finish rolling temperature, and finish rolling thickness; The set confidence level screens out effective simultaneous point measured data and same point measured data.
[0036] S12. Substituting the measured data of the simultaneous points into an iterative model to calculate the flow thickness of the simultaneous points;
[0037] S13, substituting the measured data at the same point and the measured data at the same point into the roll gap model to calculate the bounce thickness at the same point and the ...
Embodiment 2
[0044] On the basis of Example 1, as Figure II The flow chart of calculating the simultaneous point flow thickness in the present embodiment shown includes:
[0045]S121, substituting the measured data at the same time point, and preset the forward slip value;
[0046] S122, calculating the flow thickness at the first simultaneous point according to the principle of flow balance;
[0047] S123, calculating the forward slip value according to the first simultaneous point flow thickness update;
[0048] S124, judging whether the predetermined number of iterative calculations has been reached, if yes, output the flow thickness at the same point; if no, return to S122.
[0049] The implementation process of this embodiment will be described in detail below by taking the thickness control process of the "7-stage rack" finish-rolled strip steel as an example (the racks are numbered F1-F7).
[0050] After obtaining the required simultaneous point measured data and the same point ...
Embodiment 3
[0106] Such as Figure 5 Shown is a schematic structural view of Embodiment 3 of a device for controlling the thickness of a finish-rolled steel strip according to the present invention, including:
[0107]The data acquisition device 51 is used to obtain the measured data at the same point and the measured data at the same point;
[0108] The data processing device 52 calculates the zero point correction value of the roll gap model and the learning coefficient of the rolling force model according to the measured data at the same point obtained by the data obtaining device 51 and the measured data at the same point;
[0109] The control device 53 adjusts the roll gap and the rolling force according to the zero correction value and the learning coefficient of the rolling force model.
[0110] The beneficial effect of this implementation is that without adding any equipment, the self-learning process of the thickness control of the finished strip is realized, the roll gap and ro...
PUM
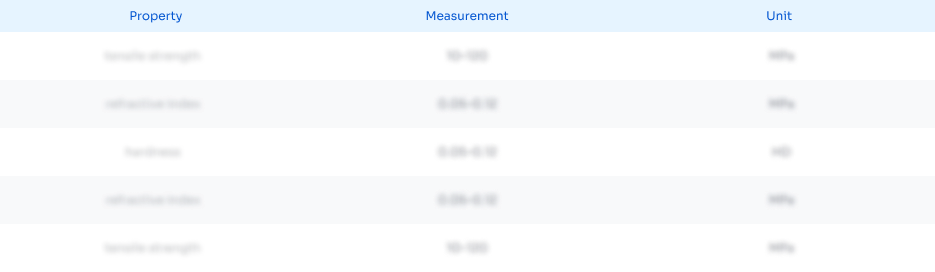
Abstract
Description
Claims
Application Information

- R&D
- Intellectual Property
- Life Sciences
- Materials
- Tech Scout
- Unparalleled Data Quality
- Higher Quality Content
- 60% Fewer Hallucinations
Browse by: Latest US Patents, China's latest patents, Technical Efficacy Thesaurus, Application Domain, Technology Topic, Popular Technical Reports.
© 2025 PatSnap. All rights reserved.Legal|Privacy policy|Modern Slavery Act Transparency Statement|Sitemap|About US| Contact US: help@patsnap.com