Six-claw double-linkage self-centering chuck
A self-centering chuck and linkage technology, applied in the direction of chucks, etc., can solve the problems of complex system and internal structure, small contact area at three points, uneven force on parts, etc., to shorten the production preparation period, and the structure is simple and compact. , Reduce the effect of card deformation
- Summary
- Abstract
- Description
- Claims
- Application Information
AI Technical Summary
Problems solved by technology
Method used
Image
Examples
Embodiment Construction
[0019] The present invention will be further described in detail below in conjunction with the accompanying drawings and specific embodiments.
[0020] Such as Figure 1 to Figure 7 As shown, a six-jaw two-linkage self-centering chuck includes a front flange 6, a front cover 7, a bottom jaw 5, a transmission assembly, a round wedge 4, a rear end cover 8, and a rear flange 9; After the end covers 7 and 8 are mutually positioned, they are connected and fixed by screws. The front and rear flanges 6 and 9 are fixedly connected with the front and rear end covers 7 and 8 respectively after being positioned. To the straight groove 801;
[0021] Such as figure 1 As shown, the transmission assembly is composed of a first slider 2, a floating lever 1 and a second slider 3, wherein the floating lever 1 is in the shape of a segment, its left and right ends are rounded, and the central angle corresponding to the segment is less than 180°. One end of the first slider 2 is a cylindrical p...
PUM
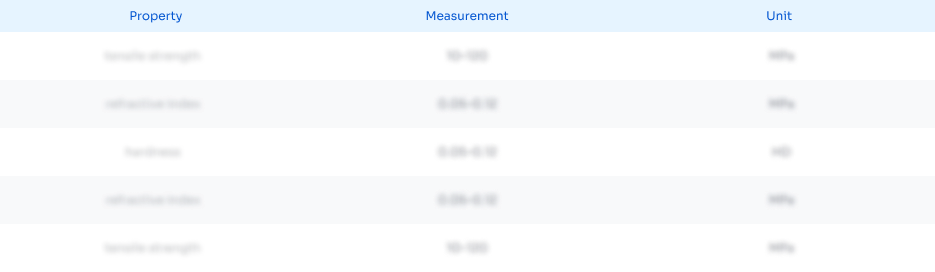
Abstract
Description
Claims
Application Information

- R&D Engineer
- R&D Manager
- IP Professional
- Industry Leading Data Capabilities
- Powerful AI technology
- Patent DNA Extraction
Browse by: Latest US Patents, China's latest patents, Technical Efficacy Thesaurus, Application Domain, Technology Topic, Popular Technical Reports.
© 2024 PatSnap. All rights reserved.Legal|Privacy policy|Modern Slavery Act Transparency Statement|Sitemap|About US| Contact US: help@patsnap.com