Progressive die discharging mechanism
A technology of discharge mechanism and progressive die, which is applied in the direction of ejection equipment, metal processing equipment, forming tools, etc., can solve the problems of high unit price of parts, low production efficiency, and lack of competitiveness, and achieve high-precision fixed distance system, production The effect of improving efficiency and improving competitiveness
- Summary
- Abstract
- Description
- Claims
- Application Information
AI Technical Summary
Problems solved by technology
Method used
Image
Examples
specific Embodiment approach
[0030] figure 1 It is a part layout diagram of the products produced by the present invention.
[0031] Such as figure 1 Shown: product a1 and product b2 are two left-right mirror-symmetrical parts, which are transferred through a straight-line middle belt. The material belt passes through a series of punching and cutting in front of the mold to complete all the processes before discharge. , into the progressive die discharge mechanism of the final station.
[0032] figure 2 It is a partial view of the upper die of the progressive die of the present invention; image 3 It is a partial view of the lower die of the progressive die of the present invention; Figure 4 It is the opening state figure of the progressive die described in the present invention; Figure 5 It is a closed state diagram of the progressive die of the present invention; Image 6 for Figure 4 Enlarged view of Part A of ; Figure 7 for Figure 5 Enlarged view of Part B of ; Figure 8 For utilizing ...
PUM
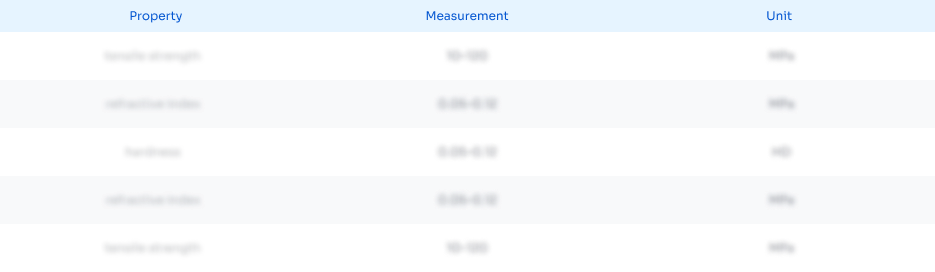
Abstract
Description
Claims
Application Information

- R&D
- Intellectual Property
- Life Sciences
- Materials
- Tech Scout
- Unparalleled Data Quality
- Higher Quality Content
- 60% Fewer Hallucinations
Browse by: Latest US Patents, China's latest patents, Technical Efficacy Thesaurus, Application Domain, Technology Topic, Popular Technical Reports.
© 2025 PatSnap. All rights reserved.Legal|Privacy policy|Modern Slavery Act Transparency Statement|Sitemap|About US| Contact US: help@patsnap.com