Large traction wriggling propulsion micro-pipeline robot
A pipeline robot and traction force technology, applied in pipeline systems, micro-manipulators, manipulators, etc., can solve the problems of difficult reduction of structure size, poor robot traction capacity, poor passability at elbows and U-shaped pipes, etc. It is easy to retreat and has the effect of good adaptability to changing pipe diameters.
Inactive Publication Date: 2010-12-01
NAT UNIV OF DEFENSE TECH
View PDF0 Cites 0 Cited by
- Summary
- Abstract
- Description
- Claims
- Application Information
AI Technical Summary
Problems solved by technology
Micro-pipeline robots are usually used for the detection of complex pipelines. They need to carry many related detection sensors, power supplies and communication devices. Wired robots also need to carry the weight of cables, which requires micro-pipeline robots to have a large load capacity. However, the current similar In the product, because the friction force driving the robot movement is not easy to increase, the load capacity is limited, and the traction ability of the robot is poor; at the same time, there are a lot of bent pipes and U-shaped pipes in the working environment of the robot, and due to corrosion, fatigue, Due to pipe joints and other reasons, there is a change in pipe diameter, which requires that the micro-pipeline robot has a small radial dimension, and has better passability at bends and U-shaped pipes and strong adaptability to variable pipe diameters. However, the current similar products There are ubiquitous defects such as difficult reduction in structural size, poor ability to adapt to pipe diameter changes, and poor passability at bends and U-shaped pipes.
Method used
the structure of the environmentally friendly knitted fabric provided by the present invention; figure 2 Flow chart of the yarn wrapping machine for environmentally friendly knitted fabrics and storage devices; image 3 Is the parameter map of the yarn covering machine
View moreImage
Smart Image Click on the blue labels to locate them in the text.
Smart ImageViewing Examples
Examples
Experimental program
Comparison scheme
Effect test
Embodiment Construction
the structure of the environmentally friendly knitted fabric provided by the present invention; figure 2 Flow chart of the yarn wrapping machine for environmentally friendly knitted fabrics and storage devices; image 3 Is the parameter map of the yarn covering machine
Login to View More PUM
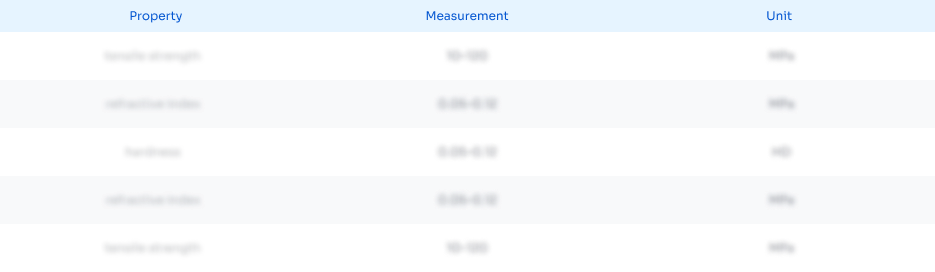
Abstract
The invention relates to a large traction wriggling propulsion micro-pipeline robot which comprises a first supporting mechanism, a second supporting mechanism and a telescopic driving device arrangedbetween the first supporting mechanism and the second supporting mechanism; wherein, the first supporting mechanism comprises a first tension rod, a first supporting seat and a first supporting wheelset; a first guide hole which is corresponding to the first supporting wheel set is arranged on the first supporting seat, the first supporting seat is sheathed outside the first tension rod which isformed by a first taper section, a first thread section and a first sliding bar section; the smaller diameter end of the first taper section is connected with the first thread section, and the biggerdiameter end thereof is connected with the first sliding bar section; the first thread section is connected with the telescopic driving device, the first thread section is provided with a first tension nut, a first compression spring is arranged between the first tension nut and the first supporting seat, the first supporting wheel set is connected with a first supporting wheel set support pole,and the first supporting wheel set support pole passes through the first guide hole and is contacted with the first taper section. The robot has the advantages of high load capacity, strong adaptive capacity for the pipe diameter change and better passing through capacity of a bent pipe and a U-shaped pipe.
Description
Large traction peristaltic propulsion tiny pipeline robot technical field The invention relates to a tiny pipeline robot, in particular to a peristaltic propulsion tiny pipeline robot with a large traction force. Background technique In today's society, all kinds of tiny pipes (diameter less than 20mm) have been widely used in metallurgy, petroleum, chemical industry, military weaponry, nuclear power and other fields. Most of these tiny pipes are used in systems with very harsh working environments, which are prone to corrosion, fatigue damage, or potential defects to develop into cracks, which will cause leakage accidents and even cause heavy personnel and property losses, so they are used in these pipes In the process, it needs to be tested to ensure the safe, smooth and efficient operation of the pipeline system. However, the environment where tiny pipes are located is generally not directly accessible by humans, or direct intervention is not allowed, and due to the sm...
Claims
the structure of the environmentally friendly knitted fabric provided by the present invention; figure 2 Flow chart of the yarn wrapping machine for environmentally friendly knitted fabrics and storage devices; image 3 Is the parameter map of the yarn covering machine
Login to View More Application Information
Patent Timeline

Patent Type & Authority Patents(China)
IPC IPC(8): B25J7/00F17D5/02
Inventor 尚建忠罗自荣徐小军杨军宏黑沫王卓乔晋崴
Owner NAT UNIV OF DEFENSE TECH
Features
- R&D
- Intellectual Property
- Life Sciences
- Materials
- Tech Scout
Why Patsnap Eureka
- Unparalleled Data Quality
- Higher Quality Content
- 60% Fewer Hallucinations
Social media
Patsnap Eureka Blog
Learn More Browse by: Latest US Patents, China's latest patents, Technical Efficacy Thesaurus, Application Domain, Technology Topic, Popular Technical Reports.
© 2025 PatSnap. All rights reserved.Legal|Privacy policy|Modern Slavery Act Transparency Statement|Sitemap|About US| Contact US: help@patsnap.com