Full-technique non-oriented electrical steel continuous annealing test method
A technology of oriented electrical steel and test method, which is applied in the field of continuous annealing test of non-oriented electrical steel in the whole process, can solve the problems of poor repeatability of the same process, long test cycle, labor and material resources consumption, etc., and achieve optimization of online process parameters, shorten R&D cycle and the effect of reducing R&D costs
- Summary
- Abstract
- Description
- Claims
- Application Information
AI Technical Summary
Problems solved by technology
Method used
Image
Examples
Embodiment Construction
[0019] The raw material electrical steel hot-rolled coil among the present invention is rolled into the chilled coil of 0.35, 0.50, 0.65mm through cold rolling mill, obtains the 250 * 450mm rectangular template in the middle, 450mm is rolling direction, and template can not have indentation, Scratches, inclusions, holes, inclusions and other defects, then the surface is degreased, cleaned and dried for later use. After drying, the surface of the steel plate is evenly coated with high-temperature resistant and anti-oxidation coatings, and then cured and sintered, and welded on the coated surface with resistance welding. Weld 3 thermocouples on one diagonal of the template or weld 5 thermocouples on two diagonals for temperature collection. The welding position of each pair of thermocouples must be accurate, see the attached figure 1 with 2 . Put the welded thermocouple template into the MULTIPAS continuous annealing simulation unit manufactured by the German VATRON factory, st...
PUM
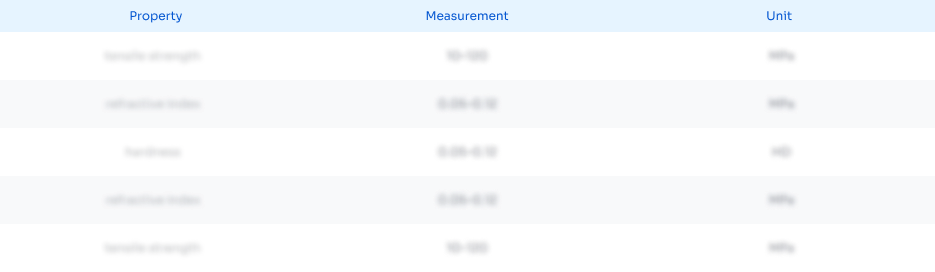
Abstract
Description
Claims
Application Information

- R&D
- Intellectual Property
- Life Sciences
- Materials
- Tech Scout
- Unparalleled Data Quality
- Higher Quality Content
- 60% Fewer Hallucinations
Browse by: Latest US Patents, China's latest patents, Technical Efficacy Thesaurus, Application Domain, Technology Topic, Popular Technical Reports.
© 2025 PatSnap. All rights reserved.Legal|Privacy policy|Modern Slavery Act Transparency Statement|Sitemap|About US| Contact US: help@patsnap.com