End milling equipment instead of ball mill
A ball mill and final powder technology, applied in grain processing and other directions, can solve the problems of low productivity, waste of resources and energy, and consumption of grinding media in Raymond mills. Effect
- Summary
- Abstract
- Description
- Claims
- Application Information
AI Technical Summary
Problems solved by technology
Method used
Image
Examples
Embodiment Construction
[0016] The present invention can be explained in more detail through the following examples. The present invention is not limited to the implementations described in the examples. The purpose of disclosing the present invention is to protect all changes and improvements within the scope of the present invention.
[0017] exist figure 1 Middle; a final grinding equipment that replaces the ball mill, including a blade feeding mechanism for feeding and sealing, a pre-grinding structure for finely divided materials, and a final grinding structure for re-rolling; the feeding The sealed blade feeding mechanism includes a blade feeder 1 and a motor B38. The lower end of the feeder 1 is connected to the upper surface of the machine cover 2, and any side of the blade feeder 1 is provided with a connecting blade feeder. The motor B38 of the impeller in the feeder 1; the pre-grinding structure for the finely crushed material, the pre-grinding structure is arranged in the upper frame 6, a...
PUM
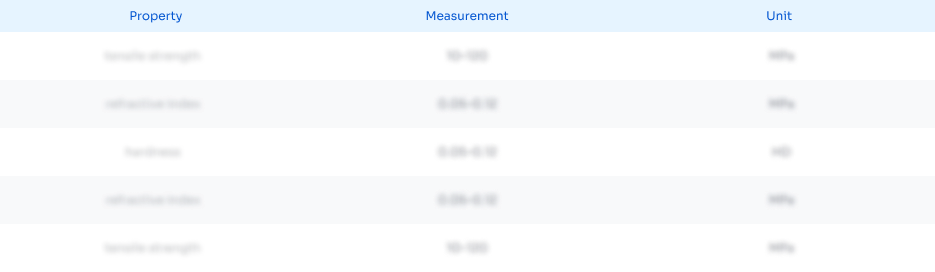
Abstract
Description
Claims
Application Information

- R&D
- Intellectual Property
- Life Sciences
- Materials
- Tech Scout
- Unparalleled Data Quality
- Higher Quality Content
- 60% Fewer Hallucinations
Browse by: Latest US Patents, China's latest patents, Technical Efficacy Thesaurus, Application Domain, Technology Topic, Popular Technical Reports.
© 2025 PatSnap. All rights reserved.Legal|Privacy policy|Modern Slavery Act Transparency Statement|Sitemap|About US| Contact US: help@patsnap.com