Flame-retardant interfacial modifier and preparation method and flame retardant polycarbonate composition
A modifier and interface technology, which is applied in the field of flame retardant interface modifier and preparation and flame retardant polycarbonate composition, can solve the problem of large amount of phosphorus flame retardant, low flame retardant efficiency and poor performance of polycarbonate Great impact and other problems, to achieve excellent impact strength and other mechanical properties, flame retardant effect is obvious
- Summary
- Abstract
- Description
- Claims
- Application Information
AI Technical Summary
Problems solved by technology
Method used
Image
Examples
Embodiment 1
[0030] The first step: add 880g of deionized water, 1.5g of tetradecylbenzenesulfonic acid and polyethylene glycol with a mass ratio of 3 in a four-necked flask equipped with a stirrer, a constant pressure dropping funnel, a thermometer and a reflux condenser. Alcohol lauryl ether composite emulsifier, add dropwise 14.8g octamethyltetrasiloxane, 64.8g diphenyldihydroxysilane, 46.2g γ-methacryloxypropylmethyldimethoxysilane , reacted at 60° C. for 5 hours, then lowered the temperature to 30° C., added dropwise 118.8 g of phenyltrimethoxysilane and reacted for 6 hours to obtain a high phenyl organopolysilsesquioxane emulsion.
[0031]Step 2: Use 0.2mol / L ammonia solution to adjust the pH value of the emulsion to 8-10, pass nitrogen into the reaction system and raise the temperature to 60°C, add 1.6g sodium dodecylbenzenesulfonate and 0.03g persulfuric acid Potassium-sodium thiosulfate initiation system, drop 30.8g hexyl acrylate, react for 8 hours to obtain polysilsesquioxane-he...
Embodiment 2
[0033] The first step: Add 880g of deionized water, 30.0g of dodecylbenzenesulfonic acid and nonylphenol with a mass ratio of 0.5 to a four-necked flask equipped with a stirrer, a constant pressure dropping funnel, a thermometer and a reflux condenser. Polyoxyethylene ether composite emulsifier, slowly drop 211.8g phenyltrimethoxysilane, 12.7g tetramethoxysilane, 25.2g dimethyldiethoxysilane, 51.8g vinyltrimethoxysilane Add and react at 30°C for 12 hours to obtain a high phenyl organopolysilsesquioxane emulsion.
[0034] Step 2: Use 2mol / L potassium hydroxide solution to adjust the pH value of the emulsion to 9-10, pass nitrogen into the reaction system and raise the temperature to 90°C, add 9.5g butyl acrylate, 0.5g dodecylbenzenesulfonate Sodium acid pre-emulsified for 1 hour, then dropwise added an aqueous solution containing 0.05g ammonium persulfate, and continued to react for 4 hours to obtain a polysilsesquioxane-butyl acrylate emulsion; add 28.4g butyl methacrylate, 4....
Embodiment 3
[0036] The first step: 120g phenyltriethoxysilane, 18.7g tetraethoxysilane, 26.6g octamethylcyclotetrasiloxane, 46.2g diphenyldiethoxysilane, 9.9g gamma-methylpropene Acyloxypropyltrimethoxysilane is mixed evenly, and one-tenth of it is added to a tank equipped with a stirrer, a constant pressure dropping funnel, a thermometer and a reflux condenser, which has added 880g of deionized water and 4.0g of dodecyl In a 2000mL four-necked flask of benzenesulfonic acid, react at 40°C for half an hour to obtain a blue polysilsesquioxane seed emulsion; add 2.0g of dodecylbenzenesulfonic acid, and add the remaining nine-tenths of The silane monomer mixture was reacted at 40°C for 8 hours to obtain a high phenyl organopolysilsesquioxane emulsion.
[0037] Step 2: Use 0.2mol / L sodium hydroxide solution to adjust the pH value of the emulsion to 9-10, pass nitrogen into the reaction system and raise the temperature to 95°C, add 0.5g sodium dodecylbenzenesulfonate, 1.0g Potassium persulfate...
PUM
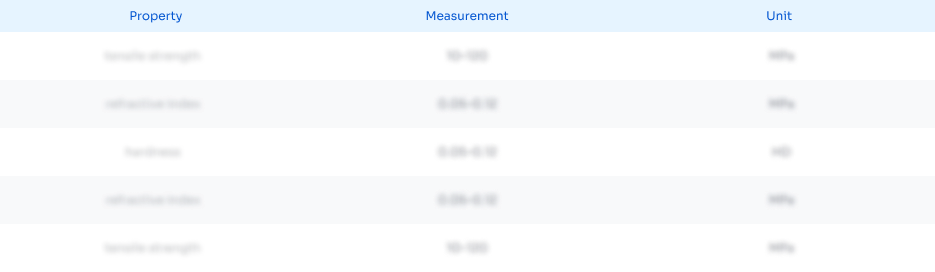
Abstract
Description
Claims
Application Information

- R&D
- Intellectual Property
- Life Sciences
- Materials
- Tech Scout
- Unparalleled Data Quality
- Higher Quality Content
- 60% Fewer Hallucinations
Browse by: Latest US Patents, China's latest patents, Technical Efficacy Thesaurus, Application Domain, Technology Topic, Popular Technical Reports.
© 2025 PatSnap. All rights reserved.Legal|Privacy policy|Modern Slavery Act Transparency Statement|Sitemap|About US| Contact US: help@patsnap.com