Tail-gas comprehensive utilization method in mercuric chloride catalyst
A mercuric chloride and tail gas technology, applied in chemical instruments and methods, separation methods, calcium/strontium/barium chloride and other directions, can solve the problems of hidden danger of secondary pollution, waste of exhaust heat, energy waste, etc., and achieve low production costs , energy saving, good effect of environmental protection
- Summary
- Abstract
- Description
- Claims
- Application Information
AI Technical Summary
Problems solved by technology
Method used
Examples
Embodiment 1
[0013] The method for comprehensively utilizing the tail gas in the production of mercuric chloride catalyst comprises the following steps:
[0014] (1) Recovery of waste heat from tail gas: Based on the production of 2 tons of dry-based mercury chloride catalyst products, the flow rate of the tail gas at 105°C discharged from the dryer is 2900Nm 3 / h, through the pre-dryer connected in series behind the dryer, the heat conduction indirectly pre-dries the wet mercuric chloride catalyst; the temperature of the tail gas discharged from the pre-dryer is 44 ° C, and the pre-drying time is 17 hours; the chlorination after pre-drying The mercury catalyst is moved into the dryer and dried to the finished product;
[0015] (2) BaCl 2 -Ba(OH) 2 Solution countercurrent scrubbing: the tail gas from the pre-dryer is mixed with the tail gas from all processes in the production process of the mercury chloride catalyst, that is, the chemical activation process (only when the mercury chlori...
Embodiment 2
[0018] The method for comprehensively utilizing the tail gas in the production of mercuric chloride catalyst comprises the following steps:
[0019] (1) Recovery of waste heat from tail gas: Based on the production of 2 tons of dry-based mercuric chloride catalyst products, the flow rate of 100°C tail gas discharged from the dryer is 2900Nm 3 / h, through the air preheating heat exchanger connected in series behind it, the heat conduction countercurrent indirectly preheats the air at natural temperature, so as to realize the recovery and utilization of the waste heat of the exhaust gas, and the preheated air is sent into the electric hot stove and heated to After 130°C, it is used to dry mercury chloride catalyst products. The temperature of the tail gas discharged from the heat exchanger is 43°C.
[0020] (2) BaCl 2 -Ba(OH) 2 Solution countercurrent scrubbing: the tail gas from the pre-dryer is mixed with the tail gas from all processes in the production process of the merc...
Embodiment 3
[0023] The method for comprehensively utilizing the tail gas in the production of mercuric chloride catalyst comprises the following steps:
[0024] (1) Recovery of waste heat from tail gas: Based on the production of 2 tons of dry-based mercury chloride catalyst products, the flow rate of 103°C tail gas discharged from the dryer is 2900Nm 3 / h, through the air preheating heat exchanger connected in series behind it, the heat conduction countercurrent indirectly preheats the air at natural temperature, so as to realize the recovery and utilization of the waste heat of the exhaust gas, and the preheated air is sent into the electric hot stove and heated to After 130°C, it is used to dry mercury chloride catalyst products. The temperature of the tail gas discharged from the heat exchanger is 40°C.
[0025] (2) BaCl 2 -Ba(OH) 2 Solution countercurrent scrubbing: the tail gas from the pre-dryer is mixed with the tail gas from all processes in the production process of the mercu...
PUM
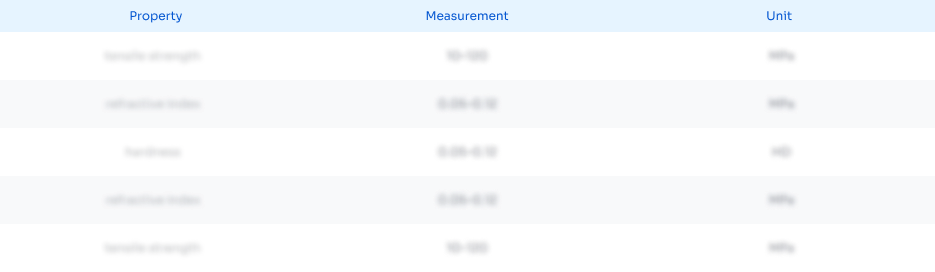
Abstract
Description
Claims
Application Information

- R&D
- Intellectual Property
- Life Sciences
- Materials
- Tech Scout
- Unparalleled Data Quality
- Higher Quality Content
- 60% Fewer Hallucinations
Browse by: Latest US Patents, China's latest patents, Technical Efficacy Thesaurus, Application Domain, Technology Topic, Popular Technical Reports.
© 2025 PatSnap. All rights reserved.Legal|Privacy policy|Modern Slavery Act Transparency Statement|Sitemap|About US| Contact US: help@patsnap.com