Helicopter rotor operation method and system
A helicopter rotor and control system technology, applied in the field of helicopter control, can solve the problems of actuators not working properly, no measurement and control scheme, no transmission mechanism, etc., shorten the development cycle, improve safety and survivability, and facilitate The effect of integration
- Summary
- Abstract
- Description
- Claims
- Application Information
AI Technical Summary
Benefits of technology
Problems solved by technology
Method used
Image
Examples
Embodiment Construction
[0033] 1. Its basic principle of the present invention sees figure 1 As shown in the figure, the driver manipulates the joystick, and the control electric signal generated by the joystick outputs control instructions through the controller, passes through the power amplifier, collector ring, rotor shaft, and is transmitted to the swing electromagnetic actuator installed on the arm of the propeller hub. The oscillating electromagnetic actuator drives the transmission rod system located inside the blade, and drives the flaps at the trailing edge of each blade to do deflection motion; as long as the torsional stiffness of the blade root is appropriate, the pitching moment generated by the flaps will be generated by the aeroelastic action. Change the pitch of the blades, so as to realize the control without automatic tilter. At the same time, the pitch angle value is fed back to the controller in real time through the pitch angle sensor to compare with the control command to obtain...
PUM
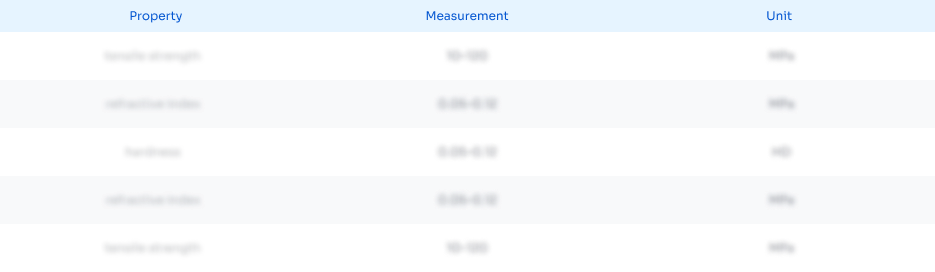
Abstract
Description
Claims
Application Information

- R&D Engineer
- R&D Manager
- IP Professional
- Industry Leading Data Capabilities
- Powerful AI technology
- Patent DNA Extraction
Browse by: Latest US Patents, China's latest patents, Technical Efficacy Thesaurus, Application Domain, Technology Topic, Popular Technical Reports.
© 2024 PatSnap. All rights reserved.Legal|Privacy policy|Modern Slavery Act Transparency Statement|Sitemap|About US| Contact US: help@patsnap.com